Summary:
The Automated Inventory Tracker is a comprehensive system that leverages advanced technologies such as object detection, GPS tracking, and 2-D mapping to streamline inventory management in outdoor areas. The system employs either object detection or RFID scanning for precise product identification. Once identified, it creates a memory map, allowing real-time tracking and visualization of all stored products. This innovative solution enhances efficiency, accuracy, and control in outdoor inventory management, providing a robust and automated approach to tracking assets.
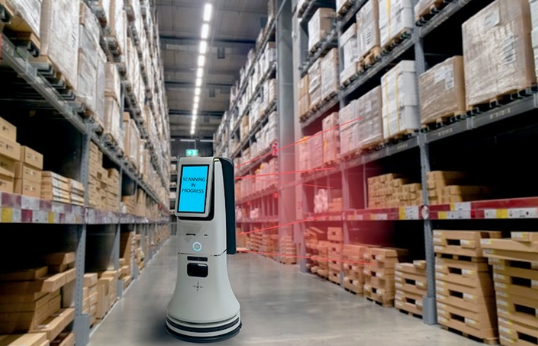
Features
1. Object Detection and Tracking
Utilizes advanced models for precise product identification and tracking.
Reduces manual intervention by automating the tracking process.
2. Accurate Product Tracking
Enables real-time tracking of product storage locations.
Facilitates easier monitoring and retrieval of stored items.
3. Reduction in Product Loss
Monitors the duration of product storage to identify potential degradation.
Notifies users about product conditions over time, reducing the risk of loss.
4. Real-time Analytics
Generates real-time reports on all stored products.
Compares product shelf-life against actual storage time for informed decision-making.
5. Improved Product Storage and Management
Identifies and notifies users of available storage space.
Offers suggestions on optimal product placement and prioritizes items for export.
6. Customizable Reports
Provides flexible report customization based on specific user needs.
Allows users to tailor reports to meet unique inventory management requirements.
7. Security and Privacy
Prioritizes data security and privacy.
Anonymizes worker identities to ensure confidentiality and compliance with privacy standard.
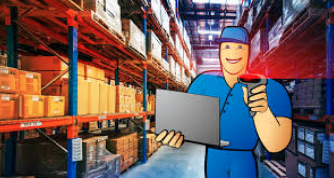
Implementation Highlights:
- Hardware Setup:
- Select appropriate sensors, such as cameras for object detection or RFID scanners. Strategically install sensors across the outdoor area to cover all storage locations.
- Install cameras on transport vehicles, along with GPS trackers, for accurate location tracking.
- Communication Setup:
- Connect sensors to a central processing unit or server for efficient data collection and analysis.
- Data Collection and Preprocessing:
- Capture real-time data from sensors, including product images or RFID tag information.
- Validate and preprocess data to ensure accuracy and completeness.
- Object Detection or RFID Scanning:
- For Object Detection:
- Train a machine learning model on product images for identification. Deploy the model for real-time detection and extract relevant information.
- For RFID Scanning:
- Attach RFID tags to each product.
- Use RFID scanners to read tag information and extract product details.
- For Object Detection:
- Memory Mapping and Storage:
- Design a structured format for the memory map.
- Store processed data in the memory map, associating products with unique identifiers and locations.
- Data Analysis and Visualization:
- Analyze product movement, storage patterns, and utilization using memory map data.Derive insights for optimal product placement, storage efficiency, and inventory management.
- Create visual representations of the memory map data for easy interpretation.
- Real-time Monitoring and Alerts:
- Implement a system for continuous updating of the memory map based on sensor data.
- Set up alerts and notifications for anomalies, such as misplaced products or low stock levels.
- Integration and Accessibility:
- Develop an interface or application for users to access and interact with memory map data.
- Integrate memory map data with existing inventory management or supply chain systems.
Tech-stack:
- IoT Sensors and Devices: To gather real-time data from production lines, machinery, and inventory.
- Artificial Intelligence (Pytorch/TensorFlow): For object detection, worker monitoring, and optimizing machinery through data analysis.
- Web and Mobile Application Development (React/Angular for web, React Native for mobile): To provide user-friendly interfaces for real-time monitoring and reporting.
- Database (MongoDB/MySQL): To store structured and unstructured data related to production and inventory.
Application:
The Automated Inventory Tracker provides users with efficient outdoor inventory management through advanced technologies. Key applications include reduced manual labour, optimized storage, prevention of product loss, real-time analytics, enhanced security, supply chain optimization, improved customer service, and easy integration into existing systems. The system offers adaptability across various industries, ensuring a versatile and streamlined solution for user