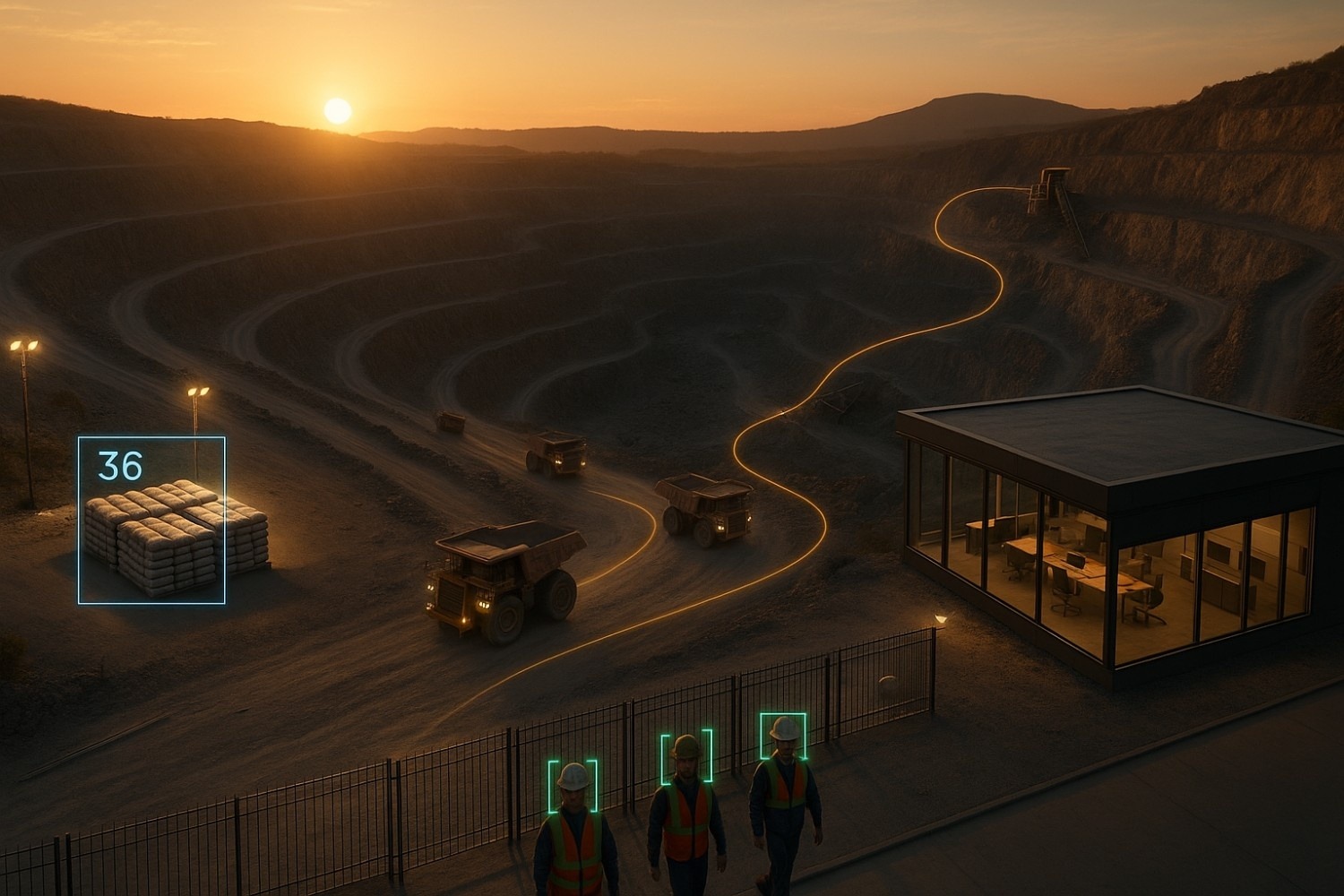
1. The Challenge
Context: Complex Mining Operations in a Harsh Environment
Mining companies operate vast sites with large workforces, heavy machinery, and valuable materials. A lead mining operation in Jeddah, for example, must manage cement stockpiles, hundreds of workers, and fleets of vehicles across remote, rugged terrain. Traditional oversight methods struggle to keep pace. Manual record-keeping and human monitoring in such environments are prone to error, delays, and blind spots. Harsh conditions (heat, dust, and 24/7 operations) further complicate consistent oversight, creating gaps that impact safety, security, and productivity.
Key Operational Challenges
- Inventory Shrinkage & Slow Reporting: Critical materials like cement bags often get lost to theft or miscounts. Relying on manual inventory logs means discrepancies might not be caught until audits, resulting in “inventory shrinkage” (loss of stock) that costs businesses billions globally. A lack of real-time visibility also delays response to theft or stock-outs.
- Inaccurate Attendance & Access Control: Keeping track of who is on site is difficult with traditional punch cards or ID badges. These systems are vulnerable to buddy punching (one worker clocking in for another), a form of time theft that costs employers hundreds of millions per year. Remote mining sites often lack the infrastructure for reliable time-clock systems, making it easy for attendance records to be manipulated or for unauthorized persons to slip in. This undermines both payroll accuracy and site security.
- Fleet Inefficiencies & Downtime: Managing a fleet of trucks and heavy equipment across multiple pits or yards is logistically challenging. Dispatchers using radios and spreadsheets can’t continuously optimize routes or predict maintenance needs. Vehicles often idle or take suboptimal routes, wasting fuel and time. Maintenance tends to be reactive (after a breakdown), leading to costly downtime. Traditional fleet management relies heavily on manual oversight and lacks the predictive, real-time optimization that modern AI can provide. The result is lower productivity, higher operating costs, and increased safety risks due to unscheduled failures or poor coordination.
These pain points highlight the need for smart AI solutions for mining industry that can automate monitoring, reduce human error, and deliver actionable insights in real time.
2. The Concept : AI Solutions for Mining Industry
Vision: In response to these challenges, Softlabs Group proposes an integrated AI-driven solution that combines three powerful modules working in unison. This holistic system automates inventory monitoring, personnel tracking, and fleet logistics – creating a digital nervous system for mining operations. By leveraging cameras, sensors, and intelligent software, the solution aims to provide real-time visibility and control over materials, workforce, and vehicles, far beyond what manual methods can achieve.
Integrated Solution Modules: The platform consists of three interconnected AI modules addressing each challenge area:
- AI-Driven Cement Bag Inventory Tracking: This module uses advanced Computer Vision (CV) (technology enabling computers to interpret and understand visual images) to monitor cement bags and other material stockpiles continuously. Cameras placed in storage areas or loading zones automatically count cement bags and detect any removal or addition. The system logs inventory levels in real time and flags anomalies – for example, if bags go missing outside of scheduled usage, or if a loading truck’s count doesn’t match the dispatch records. By catching discrepancies instantly, it helps reduce theft and miscounts, ensuring that stock reports are always accurate and up-to-date.
- Facial Recognition for Attendance & Access Control: A biometric access system replaces outdated punch clocks and ID cards. As workers enter the site or designated zones, a camera or tablet terminal scans their face. Facial Recognition (AI-driven identification of a person based on facial features) verifies each employee’s identity against a secure database in seconds. Upon a positive match, it automatically logs the entry time (or exit when they leave) and can even unlock turnstiles or doors for authorized personnel. This ensures only authorized staff gain access and creates an accurate, tamper-proof attendance record. Employees must be physically present to clock in, eliminating buddy punching and time fraud. The system provides a live attendance dashboard for supervisors, showing who is on-site and where, which is vital for both operational planning and emergency safety.
- TensorFleet: AI Fleet Logistics Automation: TensorFleet is Softlabs Group’s proprietary AI-powered fleet management system designed specifically for heavy industrial operations. It uses data from GPS trackers and onboard IoT sensors installed in haul trucks, excavators, and service vehicles across the mining site. By continuously analyzing GPS telemetry (location and movement data transmitted by vehicles) along with vehicle performance metrics, TensorFleet provides real-time tracking and intelligent coordination of the fleet. It can automatically suggest optimal haul routes, dispatch schedules, and loading sequences based on current conditions. For example, the AI might detect that a particular route from the pit to the processing plant is congested or longer, and redirect trucks to a shorter path, saving cycle time and fuel. It also monitors driver behavior (speed, idling, harsh braking) and engine data to schedule predictive maintenance (using AI to predict and prevent equipment failures) before a breakdown occurs. In essence, TensorFleet acts as a digital logistics brain that optimizes fleet usage, reduces idle time, and improves safety by ensuring vehicles operate within optimal parameters.
Unified Platform: These modules are designed to integrate seamlessly. They can operate as standalone components or as a unified platform sharing data. For instance, inventory tracking alerts can be linked with access logs (to know who was near the stock at a given time) for investigative security, and attendance data can feed into TensorFleet to correlate which drivers were operating which vehicles. By combining the three AI modules, the mining company gains a 360° view of operations – from the flow of materials to the movement of people and machines – with all systems reporting to a central control dashboard. The concept is to empower mine managers with timely, factual insights and automated controls, replacing guesswork and manual paperwork with intelligent automation.
3. How It Works: The Technology Explained
The solution operates through multiple data streams and AI processing pipelines, each tuned to its specific task. Data acquisition begins from three primary sources: cameras monitoring inventory yards and entry gates, biometric devices at access points, and GPS/sensor units on vehicles. These feed into their respective AI modules, which analyze the inputs in real time and output actionable information to managers. Below is an intuitive look at each module’s workflow:
A. Cement Bag Monitoring Pipeline
- Continuous Video Capture: High-resolution CCTV or IP cameras are positioned to overlook cement storage areas, warehouses, or loading bays. These cameras feed live video streams of the stacks of cement bags into the AI system.
- Object Detection & Counting: Each video frame is analyzed by an Object Detection model (a type of CV algorithm trained to identify and locate specific objects in images) that has been trained on images of cement bags and pallets. The model detects individual bags or bundles and counts them automatically. It can distinguish cement bags from other objects or debris in the frame, ensuring an accurate count of inventory in view.
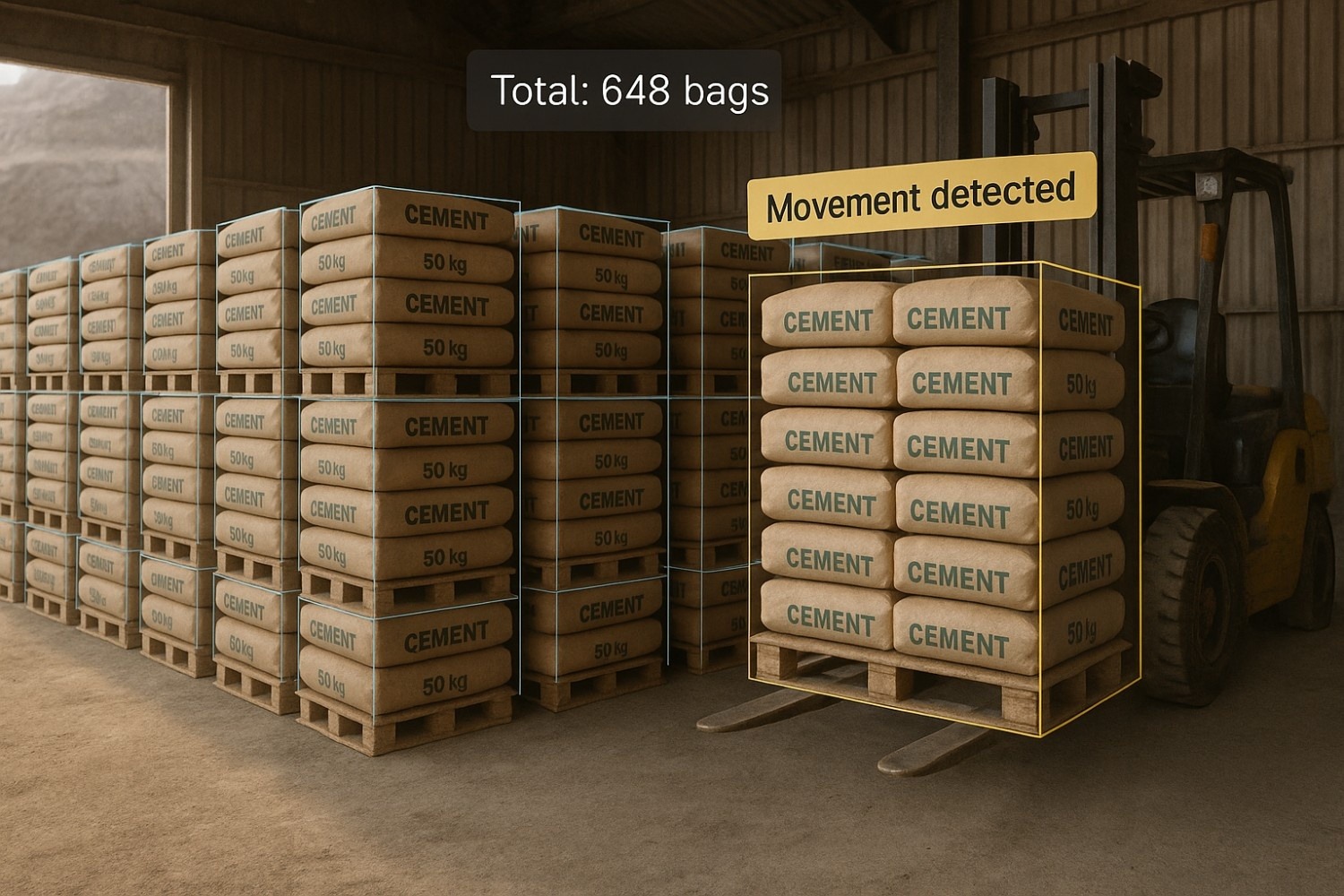
- Anomaly Detection: The system establishes a baseline count of bags and continually monitors for changes. If it sees a sudden decrease (e.g., bags being removed) or increase (new delivery) outside of expected times, it records the event. AI logic cross-references these changes with operational data – for example, checking if there’s a scheduled dispatch or delivery at that moment.
- Real-Time Alerts & Inventory Log Update: When an unscheduled or mismatched change in count occurs (possible theft or miscount), the system triggers an instant alert to managers (via a dashboard notification or even SMS/email). All changes are timestamped and logged. The inventory database is updated in real time, so supervisors can see current stock levels at any moment. These automated stock ledgers help flag unusual activity and prevent losses before they spiral out of control. At shift’s end, instead of manual counting, managers can generate a report of inventory movements verified by AI.
B. Facial Recognition Attendance Pipeline
- Biometric Data Capture: At each entry/exit point (gate or building entrance), the employee faces a facial recognition terminal – typically a camera integrated with a tablet or turnstile. As the worker approaches, the system detects a face in the video feed.
- Identity Verification: A deep learning-based facial recognition algorithm compares the live captured face to encrypted face templates stored in the company’s employee database. This algorithm analyzes unique facial features (e.g., the distance between key points on the face) to find a match. Within a second, the system confirms the person’s identity with a high degree of accuracy.
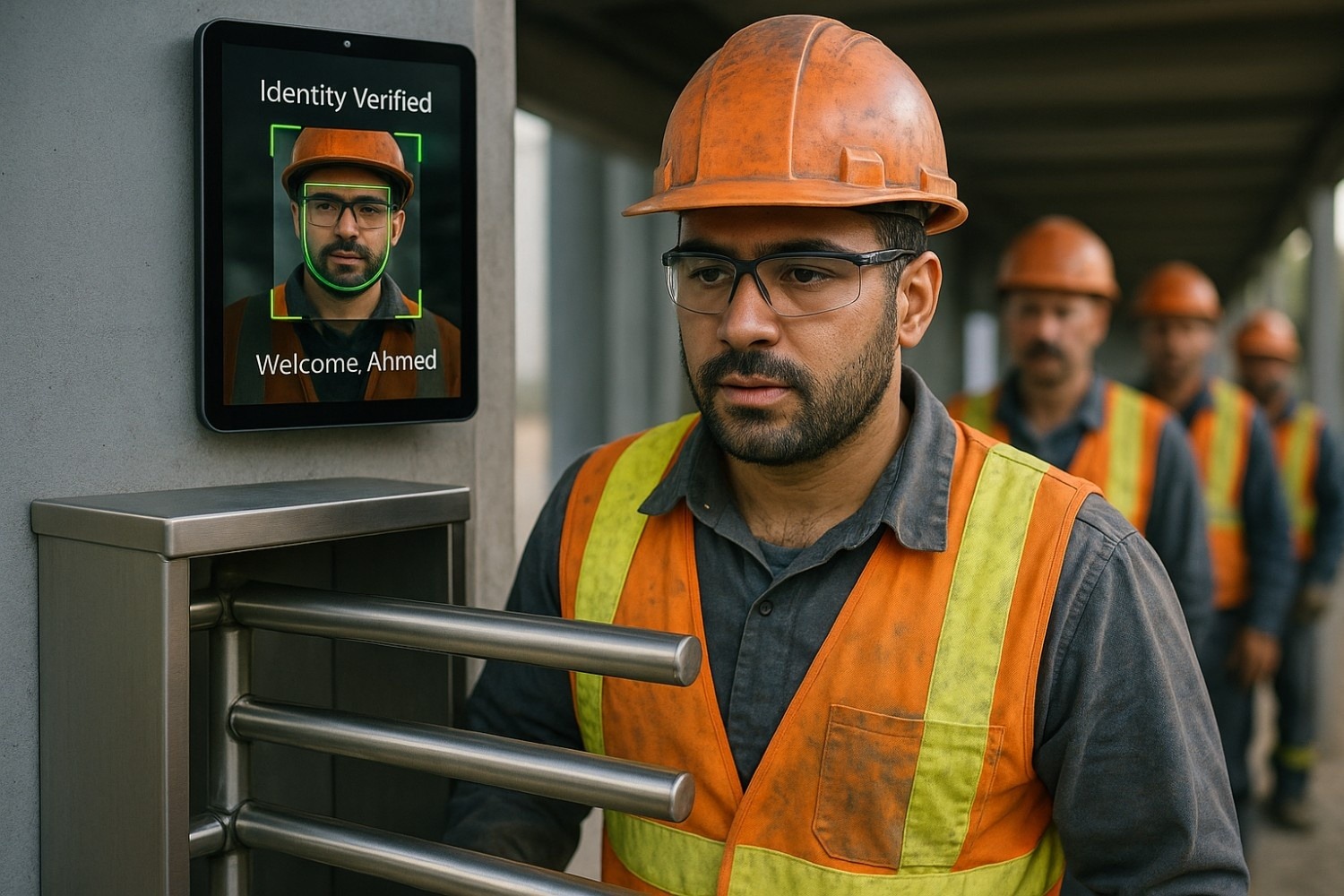
- Access Control & Logging: If the face is recognized and the person is authorized for that area, the system automatically logs the person’s name, ID, and timestamp into the attendance record. It can also interface with physical access control – for example, unlocking a turnstile or gate for that individual. One person can’t check in for another; the employee must be physically present to be recognized, which ensures the time log is honest.
- Monitoring Movement: As needed, additional cameras inside the site can track personnel movement for security (e.g., ensuring only certified workers enter hazardous zones). Every entry and exit creates a digital audit trail. Supervisors can view a live attendance dashboard showing who is currently on site, and department heads can receive automated reports (daily timesheets, overtime alerts, etc.). The system can also be set up to deny access to unregistered or blacklisted individuals, bolstering site security. All personal data and images are processed under strict privacy controls (with encryption and access logs) to maintain data protection compliance.
C. TensorFleet Logistics Automation Pipeline
- Vehicle Telemetry Ingestion: Each mining vehicle is equipped with a GPS unit and a set of IoT sensors (for engine status, fuel level, temperature, load weight, etc.). These devices continuously stream data such as the vehicle’s location, speed, direction, and various telemetry metrics over a wireless network (such as LTE or a local mesh network) to the central AI system.
- Real-Time Tracking & Visualization: The incoming GPS data is plotted on a digital map of the mining site. Fleet managers can see icons for each truck or vehicle moving in real time on this map interface. The system updates each unit’s status (e.g., “Truck A en route to Pit 3, ~5 mins to arrival”).
- AI Route Optimization: Machine Learning (ML) algorithms crunch the telemetry data along with additional inputs (road conditions, shift schedules, tonnage requirements). Using these, the system dynamically suggests optimal routes and assignments. For example, if a particular haul road is congested or a shovel at one pit is waiting, the AI might re-route trucks to balance load and reduce queue time. AI-powered platforms can analyze such patterns to find the shortest and safest paths for haul trucks, reducing travel time and fuel consumption. Dispatchers receive recommendations like “send Truck B to Loading Zone 2 instead of Zone 1 to minimize waiting.” Over time, the system learns from historical data to improve route efficiency further, much like a navigation app that adapts to traffic patterns.
- Driver Behavior & Safety Monitoring: The system also monitors driving patterns. Telemetry from accelerometers and engine diagnostics is analyzed to detect harsh braking, overspeeding, excessive idling, or signs of operator fatigue (if integrated with smart camera inside cabs). If unsafe or inefficient behavior is detected, the system can alert the driver in-cab or notify supervisors. This not only improves efficiency but also enhances safety by proactively addressing risky behavior.
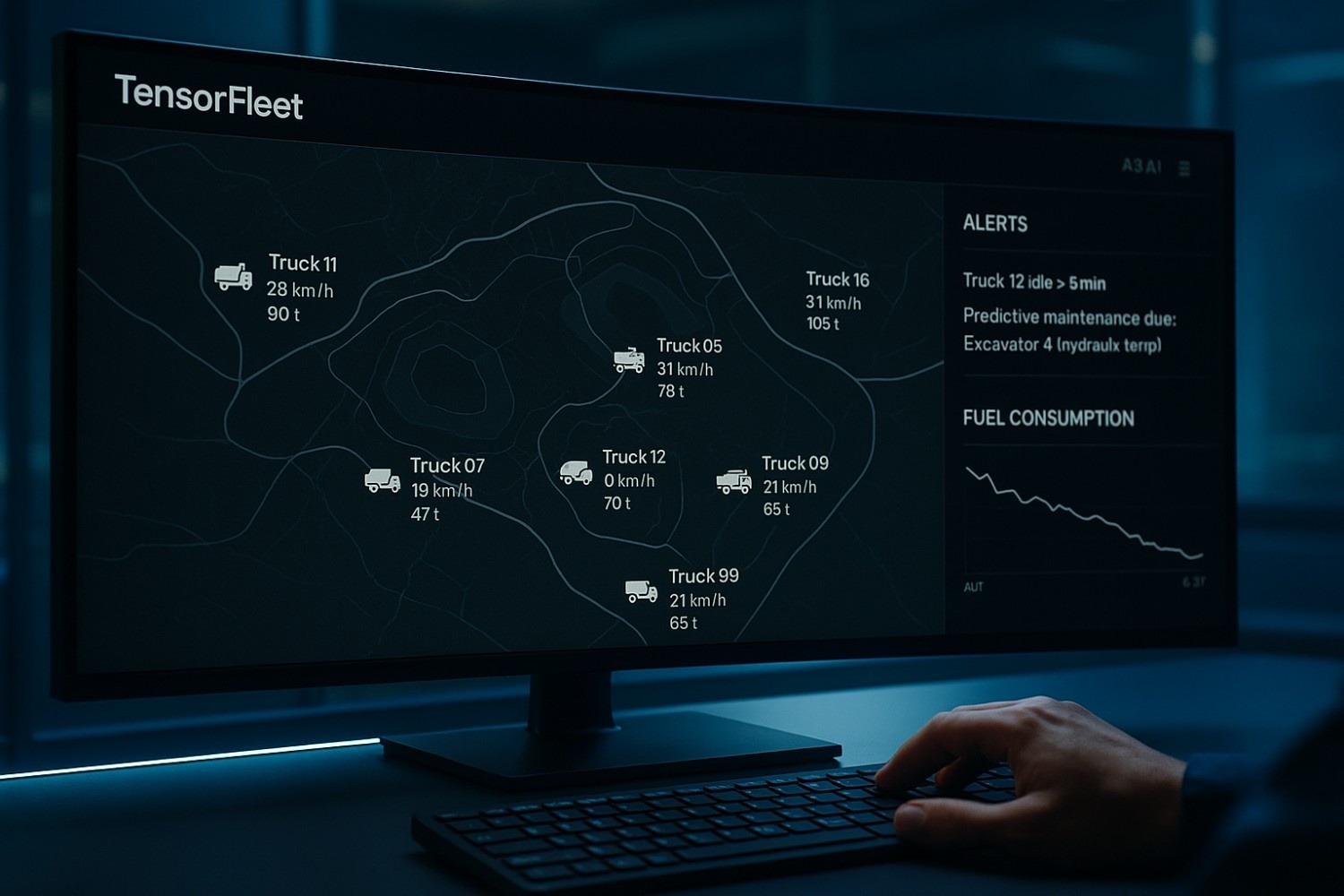
- Predictive Maintenance & Asset Management: All the sensor data (engine heat, vibration, fuel usage, etc.) feeds into predictive models. These models look for anomalies or trends that indicate a vehicle might need maintenance – for instance, a gradual increase in engine temperature or vibration could predict an impending component failure. The system will alert maintenance crews to check the vehicle at the next opportunity, before a breakdown happens. By scheduling repairs proactively, the mine avoids costly unplanned downtime and extends the equipment life.
- Dashboard and Alerts: Fleet managers interact with TensorFleet through a centralized dashboard that aggregates all this information. They can see real-time KPIs (key performance indicators) like current truck cycle times, tonnage moved per hour, fuel consumption rates, etc. The AI system flags issues (e.g., “Truck C requires maintenance in 10 hours” or “Loader waiting idle at Pit 4”) so that managers can take immediate action. Over time, all collected data is stored, allowing analysis of trends and generation of reports to find further efficiency gains.
Ready to discuss sensors, cameras, or integration details?
4. Key Enabling Technologies
Implementing this comprehensive AI solution for mining industry requires a blend of cutting-edge technologies. Each component of the system is powered by specialized tech, as outlined below:
- Computer Vision (CV): The foundational AI technology enabling computers to interpret visual inputs from cameras. CV techniques allow the system to detect and recognize objects in images or video – from counting cement bags on a pallet to spotting a person’s face at the gate or identifying a haul truck on the road. Advanced CV models (often powered by deep learning) are trained on vast image datasets so they can “see” and understand site activities much like a human would, only faster and with tireless consistency.
- Object Detection Models: A subset of computer vision algorithms specialized for locating and identifying objects within an image. For inventory tracking, object detection models (e.g., based on architectures like YOLO or Faster R-CNN) are trained to recognize cement bags and count them in various orientations and lighting conditions. Similarly, for fleet monitoring, object detectors identify vehicles and even differentiate types (truck vs. pickup). These models output bounding boxes around detected items and can do so in real time on live video frames, forming the basis for automated counting and event detection.
- Facial Recognition Algorithms: A biometric AI technology that matches live face images to stored identities. The facial recognition in this solution uses deep neural networks to map facial features into numerical representations (embeddings), which are then compared for similarity. It typically involves two steps: face detection (finding the face in the camera view) and face identification (confirming who that face belongs to). Modern facial recognition can achieve very high accuracy, even with workers wearing safety helmets or glasses, by focusing on key facial characteristics. This module ensures secure access control and accurate attendance by reliably verifying each person’s identity in milliseconds.
- GPS and IoT Telemetry: Global Positioning System (GPS) technology is used to pinpoint the real-time location of each vehicle to within a few meters. Telemetry refers to the automatic transmission of data from remote sensors – in this case, IoT devices on vehicles send continuous streams of information (location coordinates, speed, engine status, fuel level, etc.) to the central system. The combination of GPS data with other IoT sensor data provides the raw material for the fleet optimization algorithms. Enabling technologies here include satellite navigation systems, wireless communication networks, and onboard diagnostics interfaces (for accessing engine data). This allows the AI to have a live feed of the fleet’s status across the entire mining site.
- Machine Learning & Optimization Algorithms: At the core of the AI solution are machine learning models and AI algorithms that turn raw data into decisions. These include route optimization algorithms (which may use techniques like reinforcement learning or operations research methods to find optimal paths and schedules) and predictive maintenance models (often employing anomaly detection or time-series forecasting on sensor data to predict failures). For example, TensorFleet’s analytics might use regression models or neural networks to predict fuel consumption and optimize it, and classification models to determine if a truck is likely to be overloaded. These AI-driven algorithms continuously learn from new data, improving their recommendations over time. The result is a system that not only automates tasks but also learns the patterns of the mining operation to become more effective with use.
- Data Integration & Dashboard Systems: Tying everything together is a robust backend that aggregates data and presents it meaningfully. This includes databases for storing logs (e.g., inventory counts, attendance records, vehicle telemetry history) and dashboard software accessible via web or mobile interfaces. The dashboard uses data visualization techniques (charts, maps, alerts) to help managers easily digest the AI outputs. It also provides interfaces for administrators to configure the system (such as updating the list of authorized personnel, adjusting alert thresholds, or scheduling reports). A key technology here is the Industrial IoT platform that can handle high-volume data streaming and real-time processing, often deployed on cloud servers or on-premises edge servers for faster local response. Standard protocols and integrations (like connecting to existing ERP or HR systems) ensure the AI solution meshes with the company’s current IT ecosystem rather than operating in isolation.
All these technologies work in concert. For instance, computer vision and object detection enable the eyes of the system, machine learning provides the brains for decision-making, and IoT sensors along with GPS provide continuous situational awareness. Together, they form a powerful toolkit for automating and enhancing mining sector operations through AI.
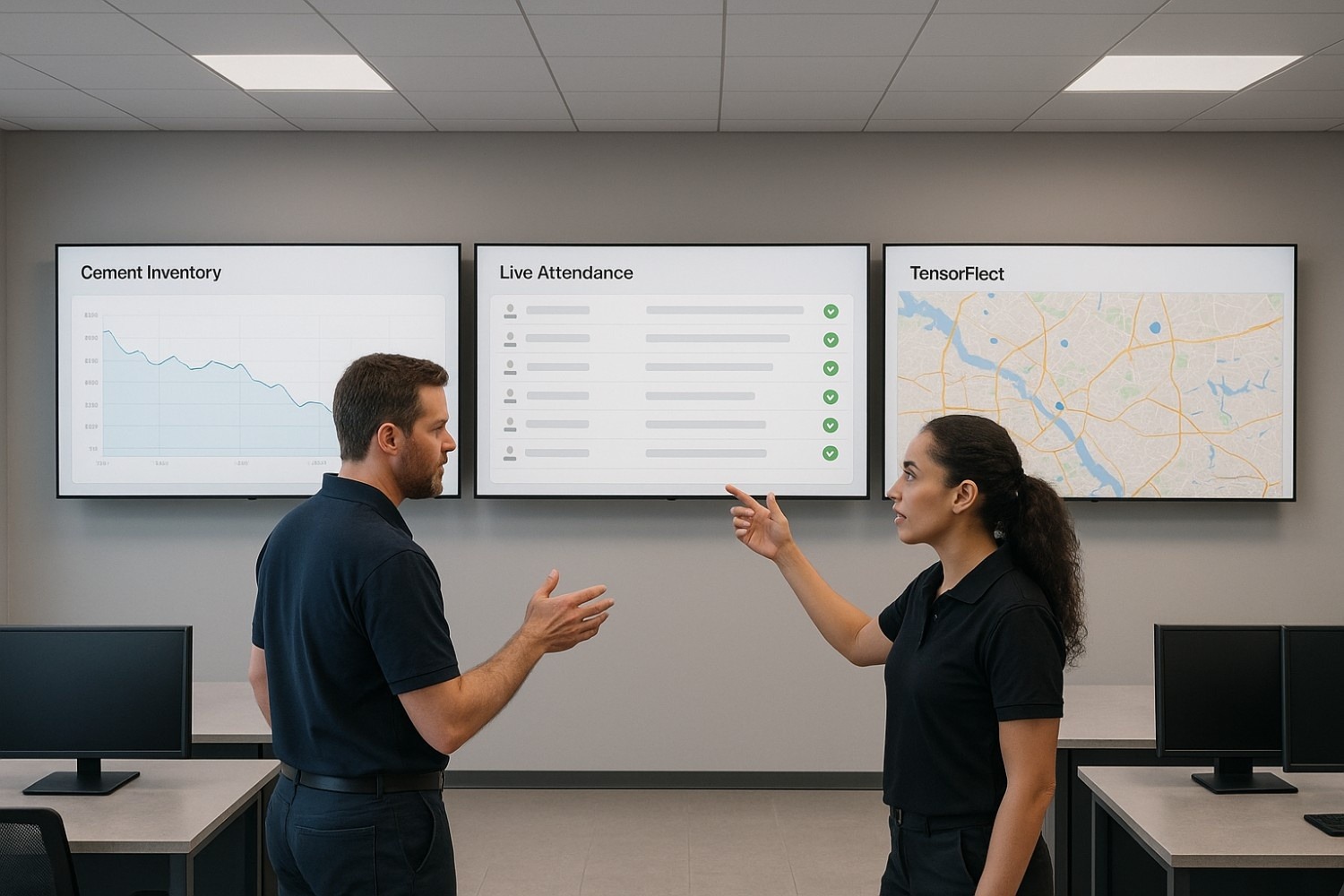
5. Potential Impact & Benefits
Adopting this integrated AI solution for mining industry can drive substantial improvements across the mining operation. By tackling previously manual and error-prone processes with intelligent automation, the mine stands to gain in many ways:
- Reduced Theft and Material Loss: Automated inventory tracking greatly diminishes opportunities for pilferage or accidental loss. The system’s real-time alerts for unusual stock changes mean that theft can be caught as it happens, deterring internal theft and preventing significant loss of valuable materials. Fewer missing cement bags translate to direct cost savings and improved accountability for how materials are used. Overall inventory shrinkage due to theft or miscounts is minimized, protecting the company’s assets.
- Accurate Records & Workforce Accountability: With facial recognition logging every entry and exit, the company gains a precise, trustworthy attendance record. This ensures employees are paid correctly for their actual work hours and eliminates disputes or investigations into timesheet fraud. In addition, knowing exactly who is on-site at any given time improves accountability and can enhance safety (for example, in an emergency evacuation, supervisors can quickly verify that everyone is accounted for). There’s also a morale benefit: diligent workers are recognized for full attendance, while any attendance issues are backed by indisputable evidence.
- Enhanced Operational Efficiency: Automation of routine monitoring tasks means staff and managers can focus on higher-value activities rather than counting bags or manually tracking trucks. Gate check-in for workers becomes faster (no queuing to sign a register or swipe cards, as face scans take seconds), so shifts can start on time without bottlenecks. At loading zones, AI-based counting of cement bags or materials loaded onto trucks speeds up the dispatch process and reduces delays. In fleet management, dynamic route optimizations lead to faster trip times and less idling, allowing more trips per shift. All these efficiency gains compound to boost overall productivity – essentially doing more work in the same amount of time or with the same resources.
- Cost Savings: The AI solution directly contributes to cost reduction in several areas. By optimizing truck routes and reducing idle time, fuel consumption drops – saving on one of the mine’s largest variable expenses (diesel fuel) ainfinite.ai, Predictive maintenance prevents major breakdowns and extends equipment life, which lowers maintenance costs and capital expenditure on new equipment. Stopping time theft (like buddy punching) ensures the company isn’t paying for hours not worked, trimming payroll bloat. And preventing material theft or spoilage means less money lost in inventory. These savings can be significant; for example, AI fleet management alone has been shown to reduce fuel costs by a double-digit percentage and maintenance costs by proactively scheduling repairs.
- Improved Safety & Security: A safer, more secure operation is a major intangible benefit. Ensuring only authorized, trained personnel are in dangerous areas reduces the likelihood of accidents. AI monitoring of driver behavior (like fatigue or speeding alerts) helps prevent accidents before they happen, protecting workers and equipment. Also, the knowledge that cameras and AI are actively monitoring can encourage everyone on site to follow safety protocols diligently. Security is strengthened by the automated access control – it’s virtually impossible for an intruder or uncredentialed individual to get onsite without detection. Moreover, in sensitive areas (explosives magazines, control rooms), facial recognition can strictly enforce access lists. The system essentially provides a continuous, automated oversight that augments EHS (Environment, Health, and Safety) personnel, leading to a more secure workplace.
- Data-Driven Decision Making: Perhaps one of the most far-reaching benefits is the wealth of data and insights generated. Managers and engineers can analyze trends such as peak usage times for cement (to optimize supply), workforce attendance patterns, or equipment utilization rates. These insights support better planning – for instance, adjusting shift schedules based on attendance data, or redesigning haul roads and stockpile layouts based on bottlenecks identified by the AI. Integrating the AI system’s data with business systems (ERP, supply chain, etc.) can unlock strategic improvements. With accurate data on hand, decisions from daily operational tweaks to long-term capital investments can be made more confidently and based on evidence, not gut feeling. This data-driven approach can yield efficiency improvements that keep the mine competitive and agile in response to market demands.
- Scalability and Standardization: Once the AI system is in place at one site, its template can be replicated or scaled to other sites or expanded in scope. This means a company can standardize best practices across all its operations – a big benefit for multinational mining firms. The AI solution’s modules can be adjusted to new contexts (e.g. tracking different materials or adding new types of sensors) relatively easily, providing a future-proof framework. Scaling up does not proportionally increase workload on managers; a single control center could oversee multiple sites’ data if needed, thanks to the high level of automation.
Overall, the integrated AI solution for mining industry acts as a force multiplier for the mining operation – boosting efficiency, cutting waste, and enhancing safety and security in a way that was not possible with traditional methods. By adopting AI for mining sector automation, companies position themselves to operate at lower cost and higher productivity, gaining a competitive edge and resilience in an industry that is increasingly looking towards technology for solutions.
See the ROI for your site in weeks, not years.
6. Important Considerations for Implementation
Deploying an AI-driven system in a mining environment requires careful planning and consideration. While the benefits are compelling, success depends on addressing practical implementation factors upfront:
- Rugged Hardware & Infrastructure: The effectiveness of computer vision and monitoring is only as good as the hardware setup. Mining sites in places like Jeddah face harsh sun, heat, dust storms, and around-the-clock operations. Cameras must be high-quality (for example, infrared/night-vision capable for 24/7 use) and housed in rugged enclosures to withstand dust, vibration, and weather. Placement is key – cameras need clear views of stockpiles and entry points without blind spots. Similarly, networking infrastructure (Wi-Fi, wired, or LTE) must be robust enough to reliably carry video streams and sensor data from remote areas of the mine to the servers. Some sites may require installation of additional access points or even edge computing units (local servers) to process data on-site if internet connectivity is limited. Ensuring power supply (with backups) for all these devices is also crucial in remote locations.
- Environmental and Site Variability: The AI models should be trained and tuned for the specific visual and environmental conditions of the mine. For instance, the appearance of cement bags might vary (different packaging or dust covering them), and lighting conditions can change drastically between the bright afternoon and flood-lit night shifts. The computer vision models need to be robust to glare, shadows, and dust interference. It’s often wise to collect sample footage from the site to fine-tune the object detection and facial recognition algorithms before full deployment. Additionally, the system must handle weather events (rain, fog) gracefully – possibly defaulting to backup procedures if cameras are obscured. Testing the AI under various conditions will help ensure it maintains accuracy in the real world.
- Data Privacy and Security: Using AI to track people (faces) and vehicles inevitably raises privacy and data protection considerations. It’s important to comply with local regulations (for example, biometric data laws) and company policies. All facial images and personal data should be encrypted and stored securely, with strict access controls. Employees should be informed about the new attendance system and its purpose to maintain transparency and trust. In practice, procedures must be in place for handling sensitive data like facial scans, ensuring they are not misused and are retained only as long as necessary. Cybersecurity is also a factor – the system should be protected against unauthorized access or tampering, as a malicious actor gaining control could be dangerous (e.g., falsely granting access or disabling alarms). Regular security audits and updates are advisable to safeguard the AI system.
- Integration with Existing Systems: For a smooth rollout, the AI solution must integrate with the mine’s current workflows and software. This means planning how to feed AI-generated data into systems like the ERP (for inventory records), the HR/payroll system (for attendance hours), or maintenance management software (for work orders triggered by predictive maintenance alerts). Rather than creating parallel processes, the goal is for the AI to enhance and streamline what’s already in place. For example, if currently inventory is tracked in a database, the AI should update that database rather than create a separate siloed database. Softlabs Group typically works with clients to map these integration points via APIs or custom adapters. It’s also important to train the on-site staff on how to use the new dashboards and interpret AI alerts as part of their daily routine. Involving end-users early (through demos or pilots) can help ensure the solution complements their work instead of disrupting it.
- Scalability and Future Expansion: Mining operations can evolve – new sites open, production scales up or down, processes change. The AI solution’s architecture should be scalable to accommodate additional cameras, more vehicles, or new modules over time. Cloud-based components can help in scaling data storage or processing power on demand. It’s wise to consider future needs during design: for instance, even if today only cement bags are tracked, perhaps in future the system might monitor fuel drums or explosives inventory as well. Ensuring the system is modular (able to accept new object detection classes or additional sensor inputs) will prolong its useful life and ROI.
- AI Model Training & Maintenance: The AI models (for vision, recognition, and prediction) are not “set and forget.” They may require initial site-specific training or calibration and periodic maintenance updates. For example, the facial recognition system will need to be updated when new employees join or if workers wear new types of safety gear that could affect recognition. The vehicle detection model might need retraining if new vehicle types or colors are introduced on site. Softlabs Group typically includes an AI model maintenance plan – monitoring the performance of the models over time and retraining them with new data as needed to maintain accuracy. This iterative approach ensures the AI keeps up with changes in the environment or operations.
- Change Management & Staff Training: Introducing AI solutions will change some job roles and processes. It’s important to prepare the workforce for these changes. Training sessions should be held so that security personnel, inventory managers, and fleet supervisors know how to interpret the AI system’s outputs (e.g., responding to an inventory theft alert or using the fleet dashboard to its fullest). Emphasize that the technology is there to assist, not replace, the on-site teams. Gaining employee buy-in can improve the adoption rate – for instance, explaining to workers that the face recognition system will speed up their entry process and ensure they’re paid accurately for overtime can turn it into a welcomed improvement rather than a feared surveillance tool.
- Initial Investment and ROI: Implementing a comprehensive AI system does require upfront investment in hardware (cameras, sensors, servers) and software development/customization. Mining companies should conduct a cost-benefit analysis to set realistic expectations. The initial costs can be significant, especially if infrastructure upgrades are needed. However, these costs must be weighed against the potential ROI from theft reduction, efficiency gains, and cost savings described earlier. Often, the system can pay for itself after a certain period (e.g., fuel savings over a couple of years might recoup the expense of the fleet management module). It’s crucial to also budget for ongoing costs like data connectivity (e.g., SIM cards for vehicle GPS units), maintenance, and occasional system updates. Framing the investment as a long-term asset for digital transformation can help secure management buy-in. Start with a pilot if necessary – proving the concept on a smaller scale can validate the benefits before scaling up to the entire operation.
By carefully considering these factors – from technical setup to organizational readiness – the mining company can ensure a smooth implementation of the AI solution. Softlabs Group emphasizes a collaborative approach during deployment: working closely with the client’s IT and operations teams to address challenges, customize the system, and transfer knowledge. Properly implemented, the AI system becomes a resilient part of the mine’s infrastructure, delivering value consistently and safely.
7. Tailoring AI for Your Unique Needs with Softlabs Group
The solution described above provides a powerful template for mining industry automation, but every mining operation has unique characteristics – from site layout and material types to specific workflows and priorities. Maximizing the benefits of AI requires adapting the system to these nuances rather than expecting a one-size-fits-all product to cover every need. This is where Softlabs Group’s expertise comes into play.
As a leader in custom AI and software development, Softlabs Group specializes in crafting bespoke AI solutions for the mining sector and other heavy industries. We understand that a surface mine in the Arabian Peninsula might face different challenges (extreme heat, specific regulatory requirements, prevalent language) compared to an underground mine in another region. Our team works closely with your engineers and managers to analyze your current processes, pain points, and goals. Whether it’s tweaking the computer vision models to recognize a particular type of sack used at your site, integrating with a legacy database, or adjusting the TensorFleet algorithms to your haul road network – we fine-tune the system to fit your operation’s DNA.
Softlabs Group’s development methodology emphasizes collaboration and iteration. We often begin with a pilot project or proof-of-concept on a smaller scale, demonstrating how the AI modules function in your environment and collecting feedback from your team. From there, we iterate – enhancing the accuracy, adding any additional features you need (perhaps you want a module for AI-powered mining equipment inspection or drone-based monitoring in the future), and ensuring the solution seamlessly integrates into your daily workflow. Our goal is to deliver technology that yields tangible, real-world value – whether that’s a measurable drop in fuel costs, faster inventory audits, or improved compliance scores during safety inspections.
Crucially, Softlabs provides training and ongoing support. We don’t just hand over the system and walk away; we partner with your staff to ensure they are comfortable and proficient in using the tools. We also offer maintenance contracts where our experts will monitor system performance, update AI models as needed (for example, periodic re-training of the facial recognition system to maintain its accuracy), and be on call to troubleshoot or extend the system as your needs evolve. In essence, we see ourselves as your long-term technology partner, committed to keeping your AI solution running optimally and evolving it in step with your business.
In the rapidly advancing world of mining technology, embracing AI solutions can be a game-changer for efficiency and competitiveness. But the true key to success lies in aligning those AI tools precisely with your operational needs and culture. Softlabs Group brings not only technical prowess in AI, IoT, and software, but also deep experience in deploying solutions in challenging industrial environments. We take pride in turning bold ideas (like a fully AI-managed mining site) into practical implementations that deliver results on the ground.