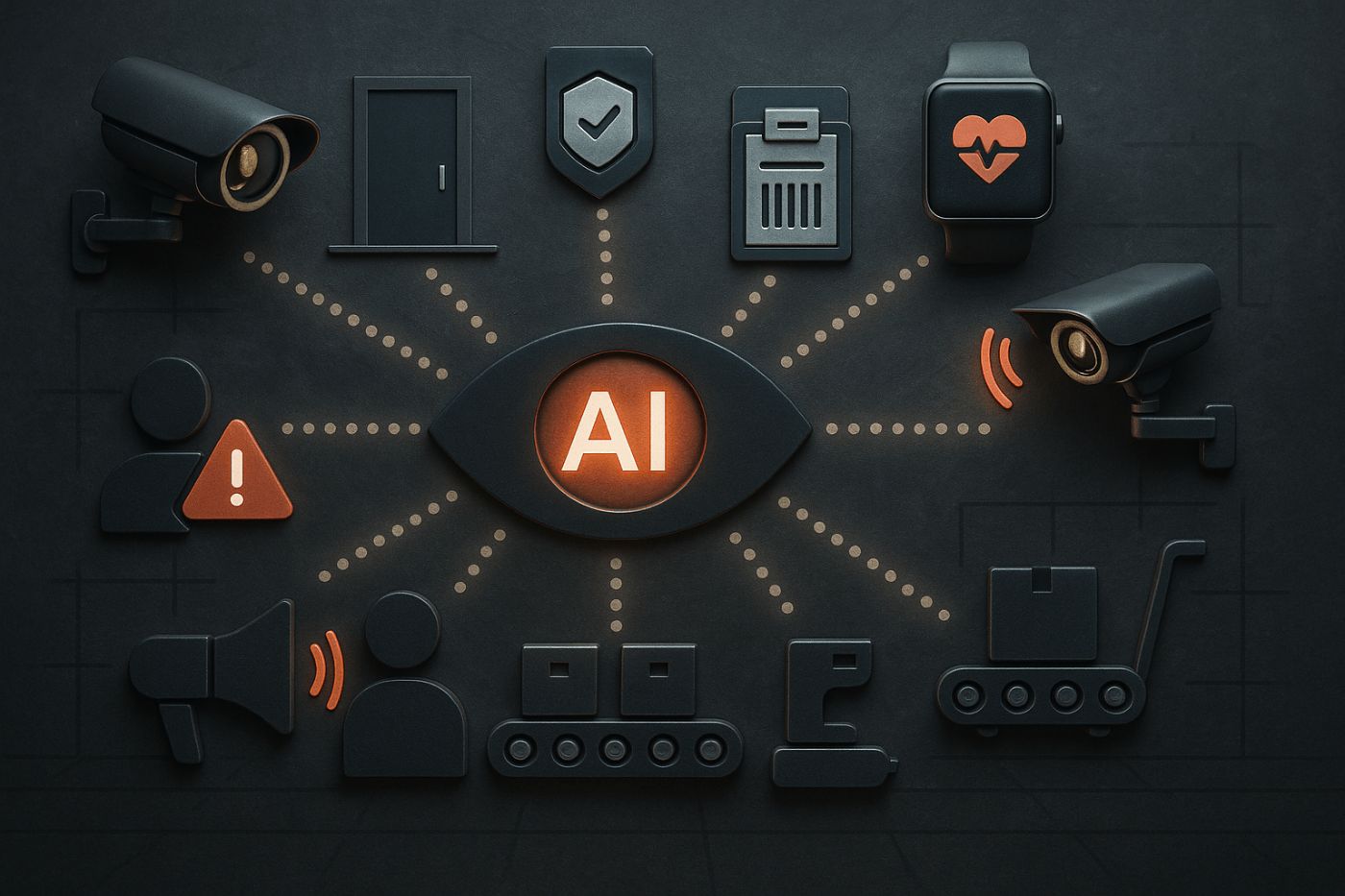
Warehouses today juggle massive throughput, demanding speed, accuracy and safety. Manual processes – from logging employee attendance to verifying inbound shipments – create bottlenecks and errors. Workers may stand in line for sign-in, data entry clerks transcribe goods receipts by hand, and security staff rely on visual checks. Meanwhile, hazardous conditions (equipment overheating, stressed operators, unauthorized access) often go undetected until incidents occur. These fragmented workflows inflate labor costs, increase shrinkage, and slow inventory turnaround. A unified AI-powered warehouse intelligence platform can tackle these issues holistically. By automating worker attendance, zone access control, GRN (Goods Received Note) processing, health and equipment monitoring, load counting, and more, AI for warehouse management streamlines operations and boosts B2B efficiency.
Context: The Warehouse Operational Landscape
In a typical warehouse, dozens of cameras and sensors already observe daily activities. However, most data stays untapped in isolated systems. For example, CCTV cameras may record faces and forklifts, but without AI they do not automatically log attendance or track vehicle usage. Likewise, inbound delivery documents (GRNs) pile up on desks for manual keying. Inventory counts often wait for end-of-day reconciliation, and equipment maintenance is reactive, based on time-schedules or emergency alerts. These siloed processes lead to delays (e.g. late GRN updates), inconsistencies (mis-counted boxes), and security gaps (undetected theft or zone breaches).
Key Pain Points Addressed by AI (Module-Specific):
- Worker Attendance: Manual timekeeping (biometric scanners or punch-cards) is slow and error-prone. AI can automatically recognize employees on CCTV to mark check-in/check-out.
- Zone Security: Restricted areas (e.g. high-rack zones, hazardous storage) often lack real-time monitoring. Unauthorized entry goes unnoticed, risking safety and theft.
- Inward GRN Processing: Paper-based goods receipts cause delays and OCR errors. Automating GRN data capture with AI speeds up inbound processing.
- Worker Health: Stress, fatigue or high blood pressure in workers can lead to accidents. Without monitoring, early warning signs are missed.
- Equipment Temperature: Overheated motors or electrical panels can cause failures or fires. Manual inspections are intermittent and reactive.
- Loading/Unloading Counts: Manual tally of bags/boxes during shipments is slow and often inaccurate, leading to inventory mismatch.
- Anti-Theft Surveillance: Human guards cannot watch all areas continuously. Small thefts or pilferage often slip through.
- Voice Alerts for Compliance: Safety and workflow non-compliance (PPE violations, traffic rules) need instant corrective feedback, which is hard without an automated system.
- Pallet Truck Telemetry: Battery-powered pallet jacks and forklifts lack detailed usage logs. Battery drain, lift usage and asset location are not tracked in real time, hampering maintenance and utilization.
Limitations of Traditional Approaches
Conventional solutions rely on manual entry and post-event analyses. Paper or badge logs, one-off thermal checks, and security patrols cannot deliver the real-time, scalable oversight warehouses need. For instance, a human guard cannot continuously audit every door and rack for unauthorized access. Similarly, spreadsheets updated at day’s end can’t prevent an overnight inventory discrepancy. Without AI-driven integration, data stays siloed – cameras record video but don’t “understand” it, and barcode scanners update inventory only at the point of scan. As a result, operations lack agility and insight.
Ready to solve these challenges with AI? Contact us to explore tailored smart warehouse solutions
The AI Solution Concepts for Warehouse Management & Automation
The vision is a modular AI platform where each module tackles a specific pain point, yet all feed into a unified warehouse intelligence system. Enterprises can deploy any combination: start with core needs (e.g. attendance and access control) and add modules like automated GRN or health monitoring over time. Each AI component uses computer vision, machine learning, or sensor data to deliver precise, actionable results. The overall objectives include eliminating manual data entry, enhancing safety, and providing real-time visibility into every critical process.
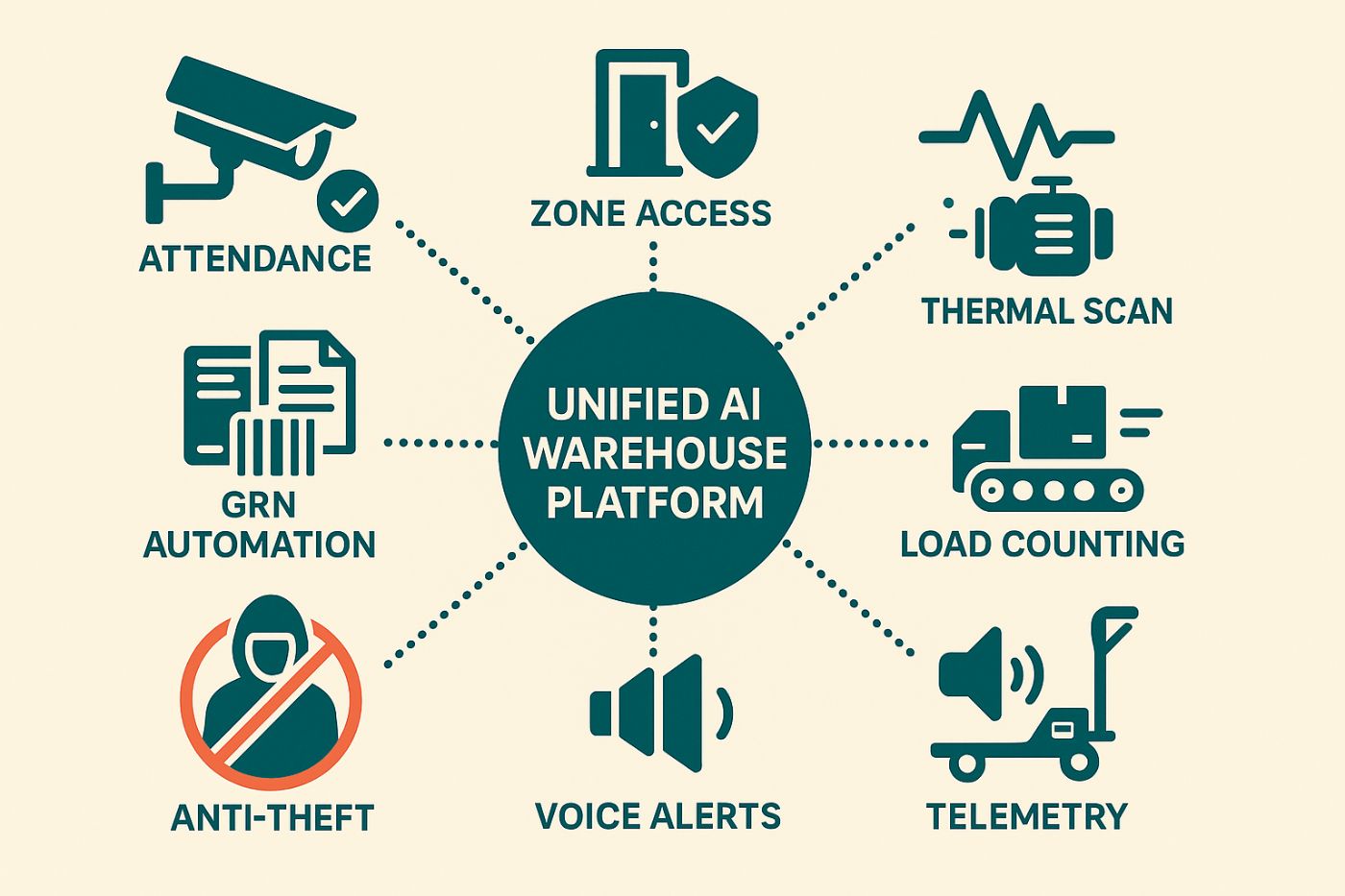
- Objective (Module 1 – Worker Attendance): Automate logging of worker entry/exit via CCTV-based facial recognition, feeding attendance data into HR/payroll.
- Objective (Module 2 – Zone Access Control): Instantly detect and alert on unauthorized persons entering restricted zones using zone-based monitoring.
- Objective (Module 3 – Inward GRN Automation): Use OCR and AI to extract text from delivery documents and match it to incoming goods, auto-updating WMS/ERP.
- Objective (Module 4 – Health Monitoring): Continuously analyze video and wearable sensor data to detect worker stress, fatigue or elevated vital signs for early intervention.
- Objective (Module 5 – Equipment Thermal Monitoring): Employ thermal imaging cameras to scan electrical panels and machines, flagging overheating components before failure.
- Objective (Module 6 – Load Counting): Deploy computer vision to detect, track, and count bags or boxes on conveyor belts or forklift loads in real time, ensuring inventory accuracy.
- Objective (Module 7 – Anti-Theft Alerts): Monitor all camera feeds to identify suspicious behavior (e.g. items removed without scanning) and raise immediate alarms.
- Objective (Module 8 – Voice Notifications): Generate automated spoken warnings (via speaker systems) when violations occur, guiding workers to corrective action.
- Objective (Module 9 – Pallet Truck Telemetry): Integrate IoT sensors on battery-powered pallet jacks to track position (RTI tracking) and measure battery usage and lift cycles, enabling predictive maintenance.
The overall objective is to enhance accuracy, efficiency, and safety across warehouse operations. By strategically applying these AI modules – either individually or in combination – businesses can reduce manual labor, prevent losses, and optimize resource use with a cohesive smart warehouse solution.
How the AI Modules Work: Technology Explained
Each module leverages specific inputs and AI techniques to produce automated outputs. Below we break down the data flow and key processes for each AI-driven component. When integrated, these modules form a powerful end-to-end warehouse intelligence platform that transforms raw data into actionable insights.
3.1 Module: Worker Attendance Monitoring
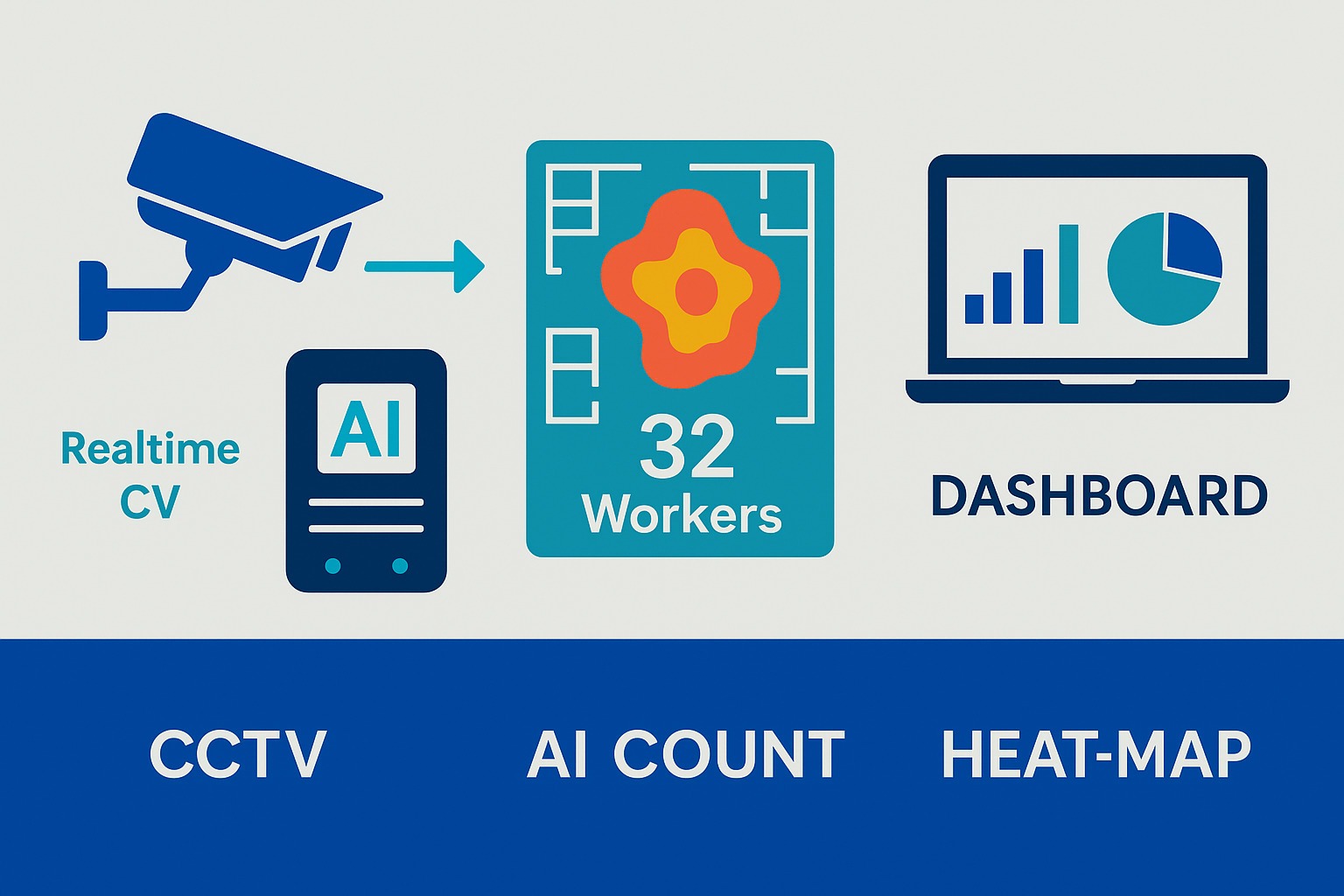
Request: Monitor the headcount of employees in real-time, potentially using an interface to track this data.
How it works in real life:
- Technology: Computer vision (CV) systems can be trained to recognize human presence and movement using the footage from existing CCTV cameras. With the right algorithms, these systems can count the number of individuals in the footage, track movements, and generate real-time reports.
- Where data will be seen: The data would be available through a dashboard or interface, where managers can see the headcount and location of employees at any given time.
Our Best Practice:
- Optimal Approach: The use of AI-driven CV for counting workers is a standard approach in many industries today. Integration with existing CCTV infrastructure is often the most cost-effective & accurate way to implement this solution.
- Our Recommendation: The use of existing CCTV infrastructure minimizes hardware investment while providing accurate real-time data.
Output & Interaction:
The platform outputs a secure attendance record (“John Doe – Checked In at 07:59”) displayed in the management dashboard. It can automatically update payroll systems or flag no-shows. By eliminating manual stamping or badge scans, it accelerates check-ins and maintains accurate logs
3.2 Module: Zone Access Detection (Unauthorized Access)
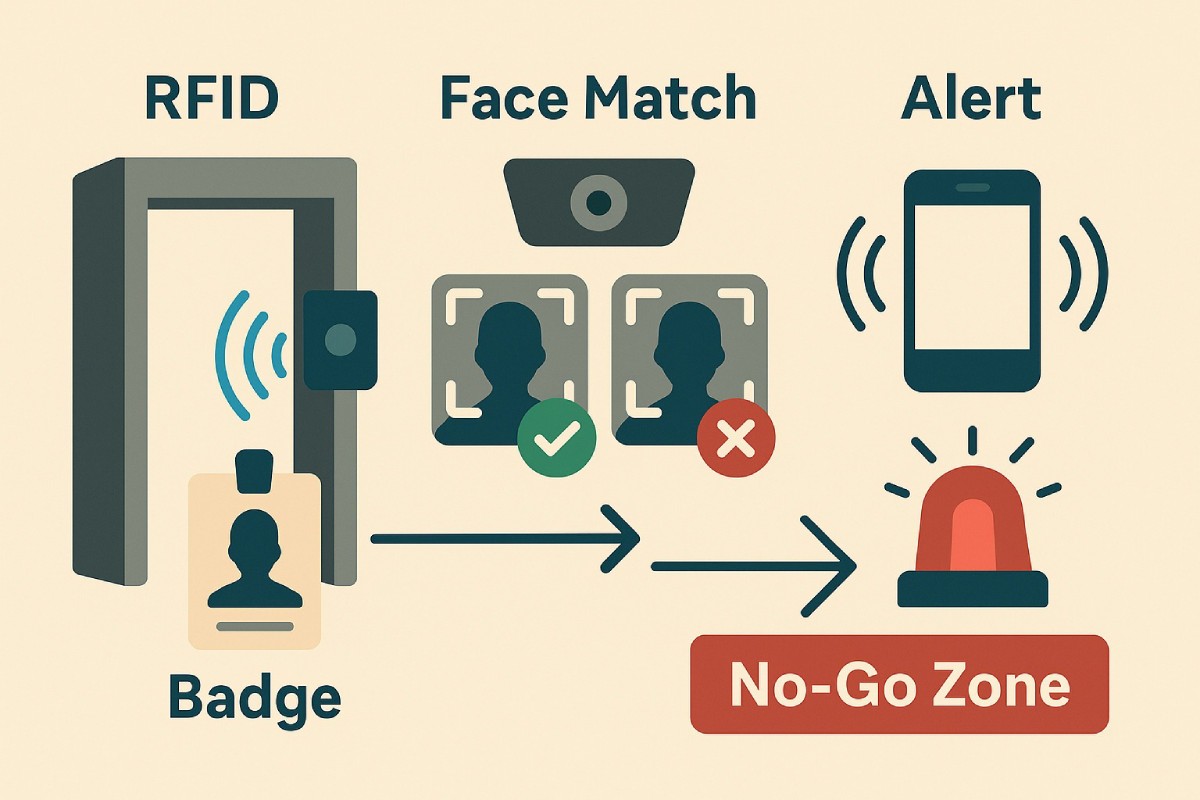
Request: Wants to know if a worker enters a restricted area and receives an alert, likely on a mobile or system interface.
How it works in real life:
- Technology: Computer vision (CV) can be used to detect specific individuals (using facial recognition or body type analysis) entering prohibited areas. Geofencing technology, combined with AI, can trigger alerts when someone breaches a restricted zone.
- Alert System: The system can trigger an alert via SMS, email, or on an employee’s mobile app or wearable device, prompting them to move out of the restricted area.
Our Best Practice:
- Optimal Approach: CV combined with AI-powered zone monitoring is a widely used solution. Integrating with an access control system (e.g., RFID or biometric systems) could improve accuracy and prevent false alarms.
- Our Recommendation: Relying solely on CCTV cameras might not be 100% foolproof—RFID/badge systems might be a more reliable way to detect unauthorized access alongside CV.
Output & Interaction:
Instant alarms are generated when unauthorized entry is detected. For example, a security operator dashboard highlights “Alert: Unrecognized Person in Zone A” or sends push notifications. This real-time monitoring and alerting can sharply reduce safety risks and theft.
3.3 Module: Inward GRN Automation
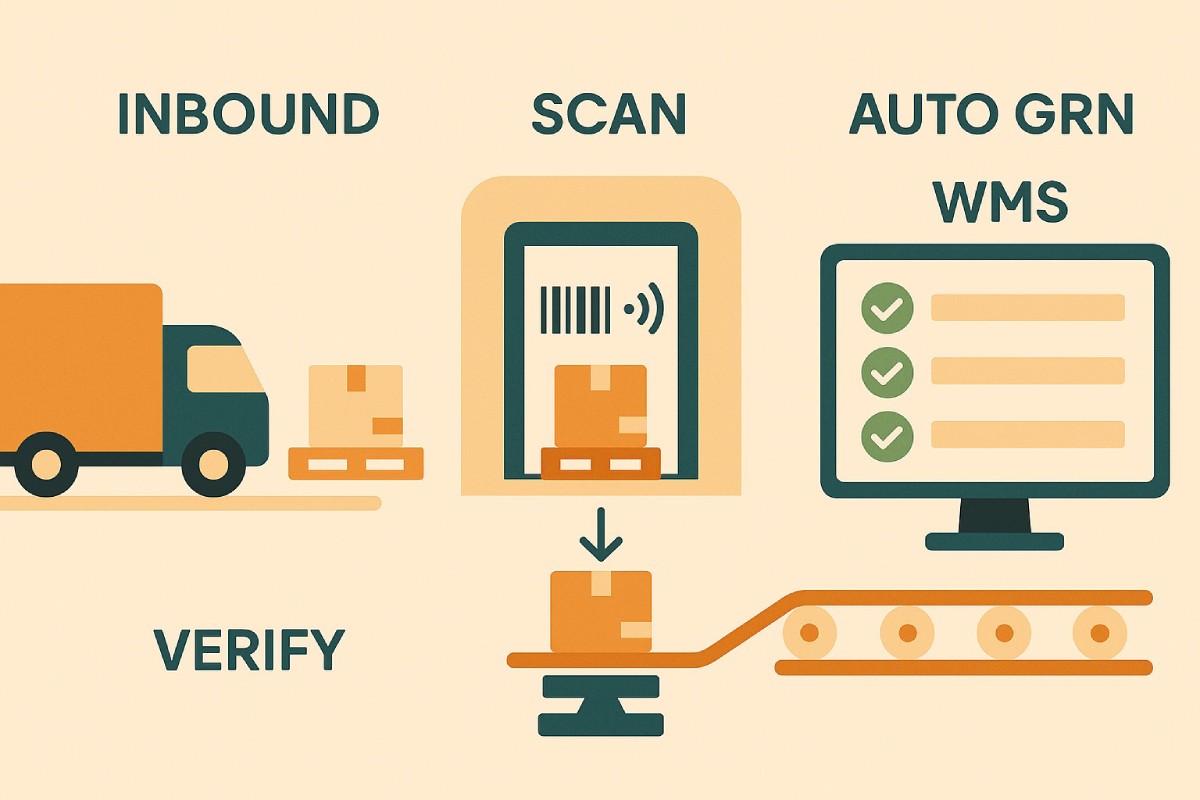
Request: Automate the process of counting and registering goods to reduce backlogs, especially for warehouses that handle products from multiple companies.
How it works in real life:
- Technology: CV systems can read barcodes, QR codes, or RFID tags on packages as they arrive at the warehouse. This data can be automatically recorded in the warehouse management system (WMS) without human intervention.
- Additional Solutions: Sensors such as weight sensors or RFID could be used to track the number of items and ensure that no goods are missed during the inbound process.
Our Best Practice:
- Optimal Approach: Integrating barcode or RFID scanning with a WMS is a standard and effective solution for automating goods receipt. Computer vision could also be used to verify the accuracy of these processes.
- Our Recommendation: CV combined with barcode or RFID scanning is the optimal and widely accepted solution. This ensures faster, more accurate processing.
Output & Interaction:
The module outputs a structured GRN record: “Item A – 150 units received, matched to PO 12345.” This automates what was manual entry, slashes processing time and errors, and feeds instantly into inventory.
3.4 Module: Worker Health Monitoring (Stress, Vital Signs)
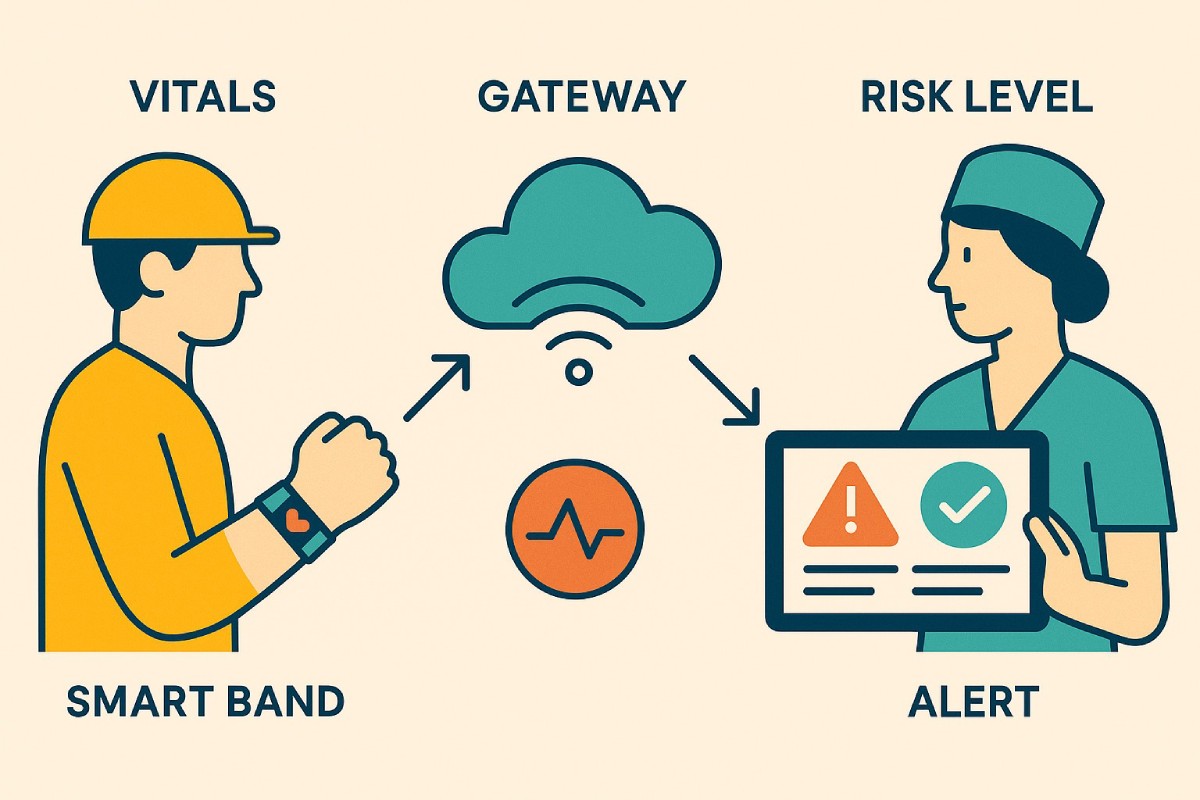
Request: The client is exploring wearables to monitor worker health or possibly computer vision for detecting stress signals. Monitoring the stress, blood pressure (BP), and heart rate of workers
How it works in real life:
- Technology: Wearable devices (e.g., fitness bands, smartwatches or our HAV safe) can monitor stress, BP, and heart rate. These devices can send data to an interface where supervisors can track health metrics.
- Alternative Approach: Computer vision could potentially identify signs of stress or discomfort (e.g., body language, facial expressions), but it would be more challenging to directly monitor BP or heart rate without wearables.
Our Best Practice:
- Optimal Approach: Wearable devices like our HAVsafe are the industry standard for monitoring health metrics like BP, heart rate, and stress levels. CV might be used to monitor behavior but is less accurate for specific metrics without a smart band
- Our Recommendation: Use wearables for health monitoring. CV can supplement this by identifying fatigue or stress-related behavior but wearables is the accepted solution
Output & Interaction:
Supervisors receive real-time alerts such as “Worker #104 shows high stress indicators.” The platform may suggest breaks or medical check-ups. Continuous monitoring helps prevent accidents due to fatigue and enables proactive health support.
3.5 Module: Equipment Temperature Monitoring
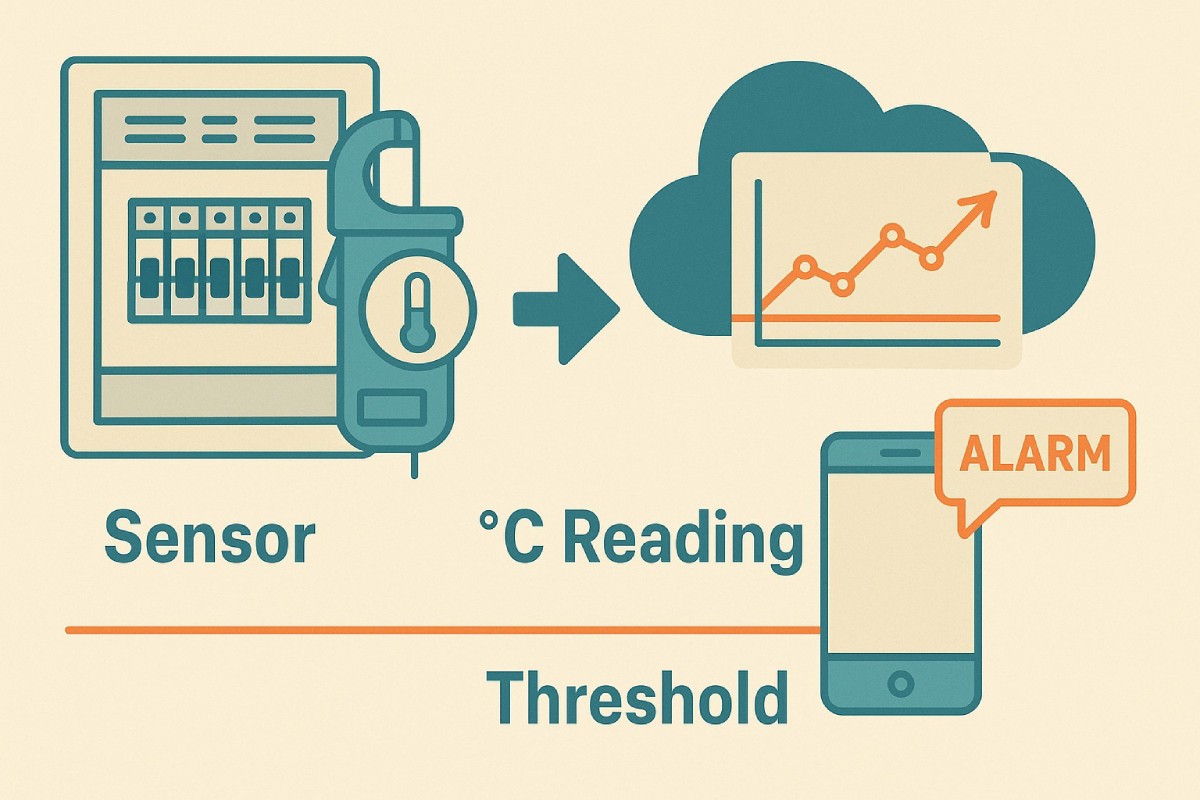
Request: The client wants to ensure that warehouse equipment is functioning optimally and without overheating.
How it works in real life:
- Technology: Temperature sensors can be installed on electrical appliances to track their temperature in real time. The data can be sent to a monitoring system that triggers alerts when temperatures exceed safe levels.
Our Best Practice:
- Optimal Approach: Using infrared sensors or thermocouples to monitor the temperature of electrical appliances is a common practice. Many industries use IoT-based sensors to track real-time temperature and ensure safety.
- Recommendation: This solution is optimal. Using temperature sensors combined with an IoT platform for monitoring is widely accepted so we are good to go with them
Output & Interaction:
When an unusual heat signature appears (e.g. a motor bearing overheating), the system triggers an alert like “Equipment ID 472 – Temperature Exceeded.” Maintenance teams can then investigate before failure. Over time, stored thermal data also supports predictive maintenance.
3.6 Module: Bags/Boxes Counting During Loading/Unloading
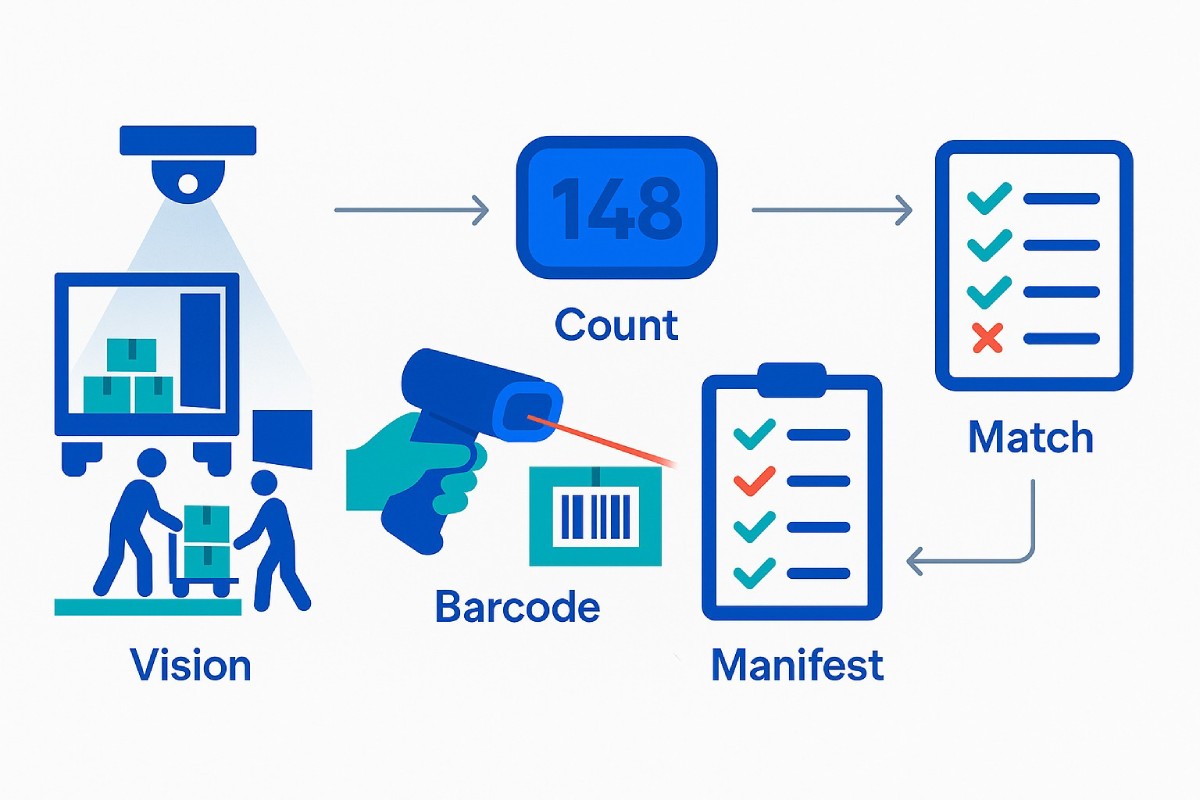
Request: The client wants a system that can automatically count items during the loading/unloading process and track the data on an interface.
How it works in real life:
- Technology: CV can detect and count items in real-time as they are moved in or out of the warehouse. Barcode or RFID scanning can be integrated to verify the count.
- Data Interface: The data would be displayed on a dashboard where supervisors can track real-time counts, identify mistakes, and analyze performance metrics.
Our Best Practice:
- Optimal Approach: CV is a great option for counting bags/boxes. Combining it with barcode/RFID scanning would ensure 100% accuracy for you.
- Our Recommendation: This approach is efficient and commonly used, especially in high-volume warehouses.
Output & Interaction:
The real-time count of items is output to inventory systems. For example, the module might report “18 boxes unloaded (expected 20) – discrepancy logged.” By automating counting, this module ensures inventory accuracy and speeds up loading processes
3.7 Module: Anti-Theft Alerts
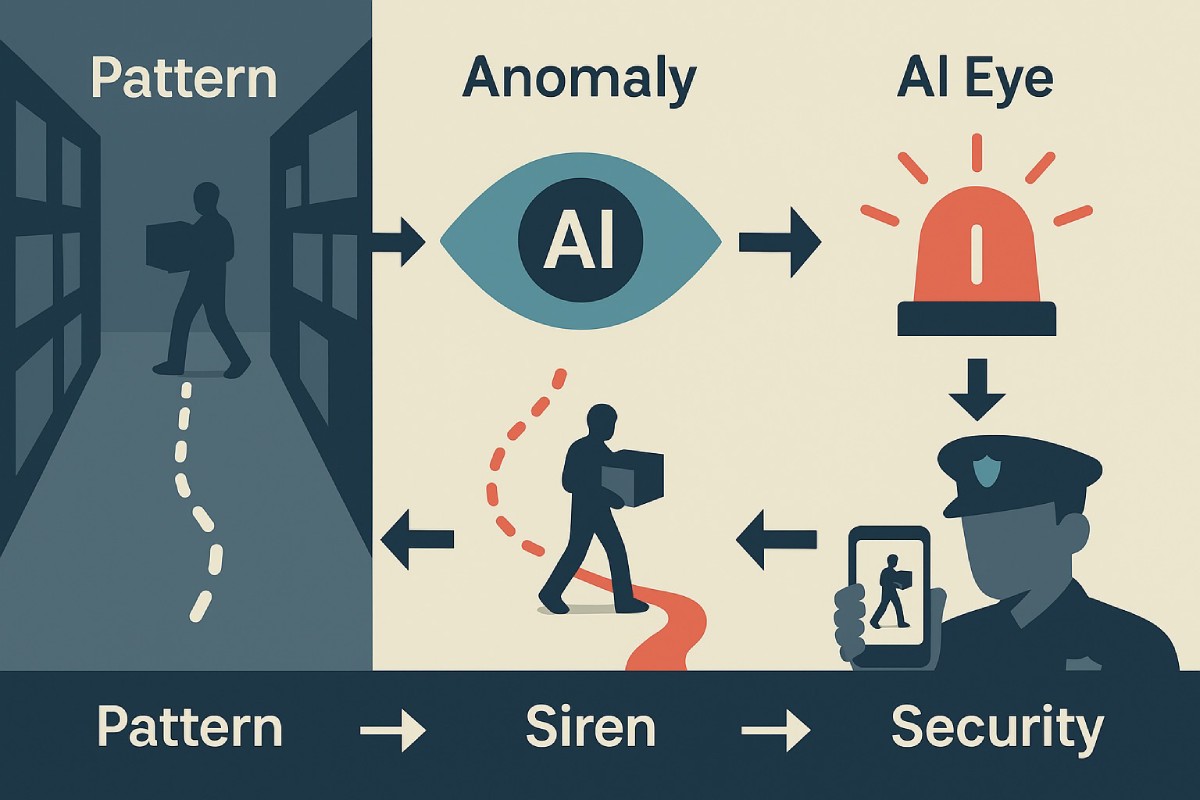
Request: An AI solution that can identify potential theft behavior based on visual cues.
How it works in real life:
- Technology: CV can analyze behavior patterns and trigger an alert if it detects suspicious behavior (e.g., someone moving unusually or attempting to hide something). This would typically be integrated into the warehouse’s security system.
- Alert System: Alerts can be sent via SMS, email, or an on-site security system.
Our Best Practice:
- Optimal Approach: Suspicious behavior detection using CV is common in high-security environments. Combining it with motion detection and behavioural analysis can improve accuracy.
- Our Recommendation: CV for anti-theft alert is a good approach, but integrating it with a more robust security system (e.g., access control, RFID) would enhance the solution for you. A double layer full proof security
Output & Interaction:
Security receives instant alerts (“Potential theft detected – check Zone B cameras”). With AI video analytics, even subtle theft attempts or tampering can be caught automatically.
3.8 Module: Automated Voice Notifications for Non-Compliance
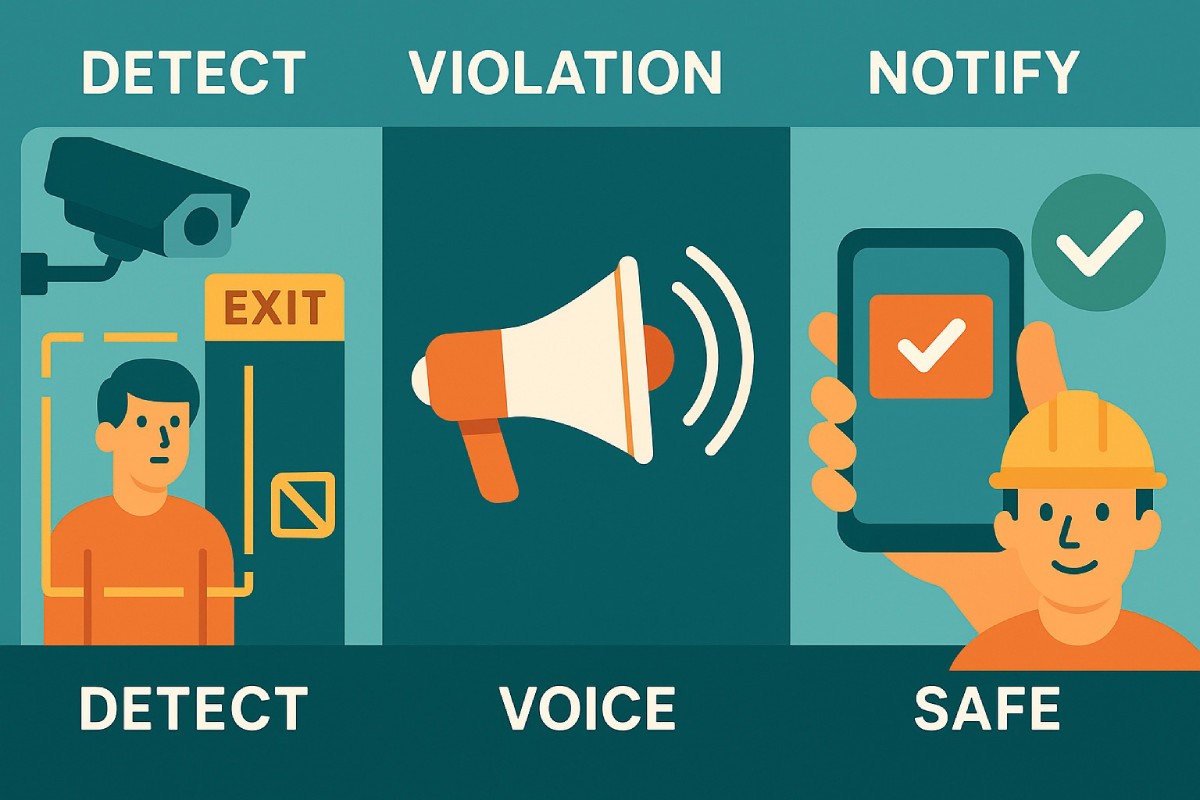
Request: The client wants workers to receive voice alerts when they engage in non-compliant behavior
How it works in real life:
- Technology: Voice alerts could be triggered by an AI system using CV to detect non-compliant behavior (e.g., safety violations). The system would be integrated with speakers in the warehouse.
- Alert System: A notification could be sent to a mobile app, on their number, wearable device, or speaker system to alert the worker.
Our Best Practice:
- Optimal Approach: Using CV combined with an audio alert system is not uncommon, but it requires careful tuning to avoid false alarms. Wearables or mobile apps can also be used for notifications.
- Recommendation: The solution is viable, but better alternatives such as text or mobile notifications to reduce distraction and confusion can also be built by us
Output & Interaction:
Workers hear clear voice prompts like “Attention: Please wear your safety helmet in this area.” By giving immediate spoken feedback, the module helps enforce safety rules without relying on human announcement.
3.9 Module: Pallet Truck Telemetry (Battery, Location, RTI Tracking)
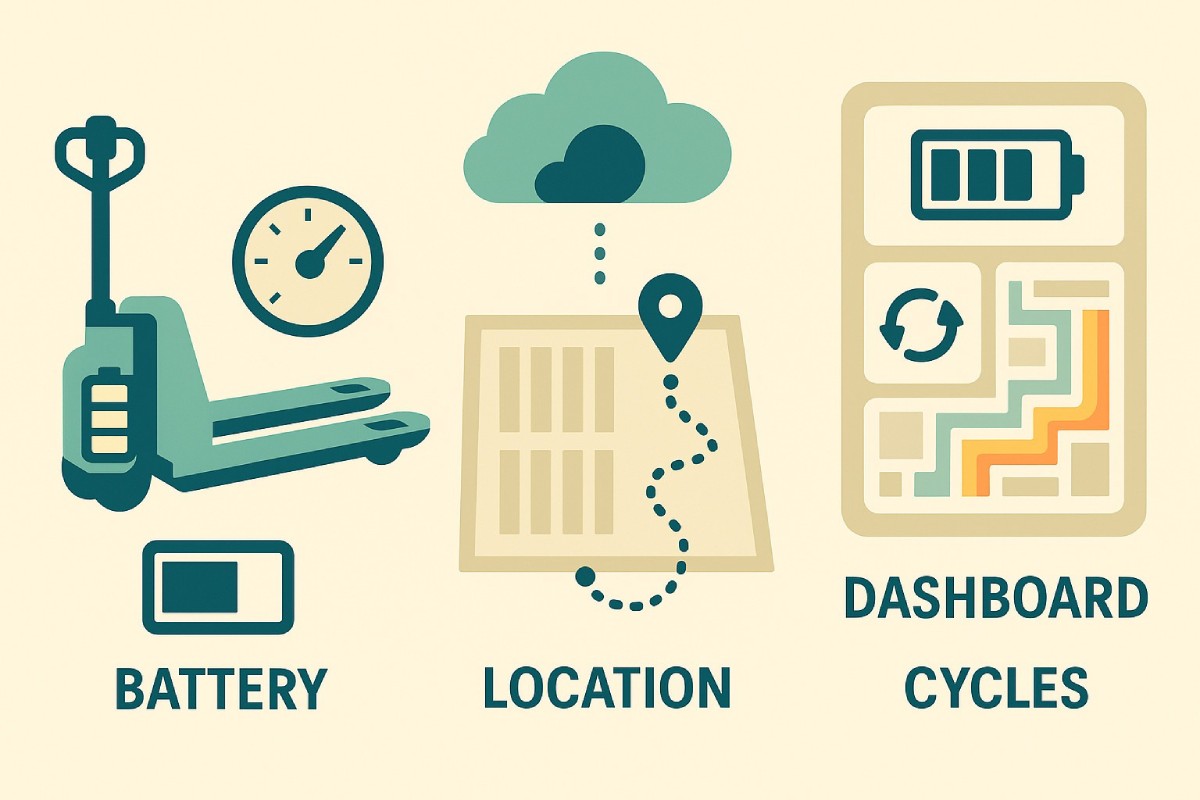
Request: The client wants to track the battery status, movement (up/down), and ensure productivity by monitoring the truck’s usage.
How it works in real life:
- Technology: Sensors can be installed to monitor battery levels and track the movement of the truck using GPS or RFID technology. The system can also measure whether the truck is carrying a load and track its location.
- Data Interface: The data would be displayed on a dashboard, showing usage patterns, battery status, and movement data.
Our Best Practice:
- Optimal Approach: IoT sensors for battery monitoring and GPS tracking are standard in warehouse management. RFID can also track the truck’s load and movement.
- Our Recommendation: This solution is efficient and widely used for equipment management and productivity tracking in warehouses
Output & Interaction:
The module outputs actionable insights: “Truck T12 – battery low at 15%,” or “Pallet #A47 has been on Truck T5 for 2 hours.” Fleet managers see real-time dashboards of all trucks and assets. This enables optimized charging schedules, replacement planning, and full traceability of material handling.
Key Enabling Technologies: Core Components
Implementing “AI for Warehouse” relies on a mix of advanced technologies:
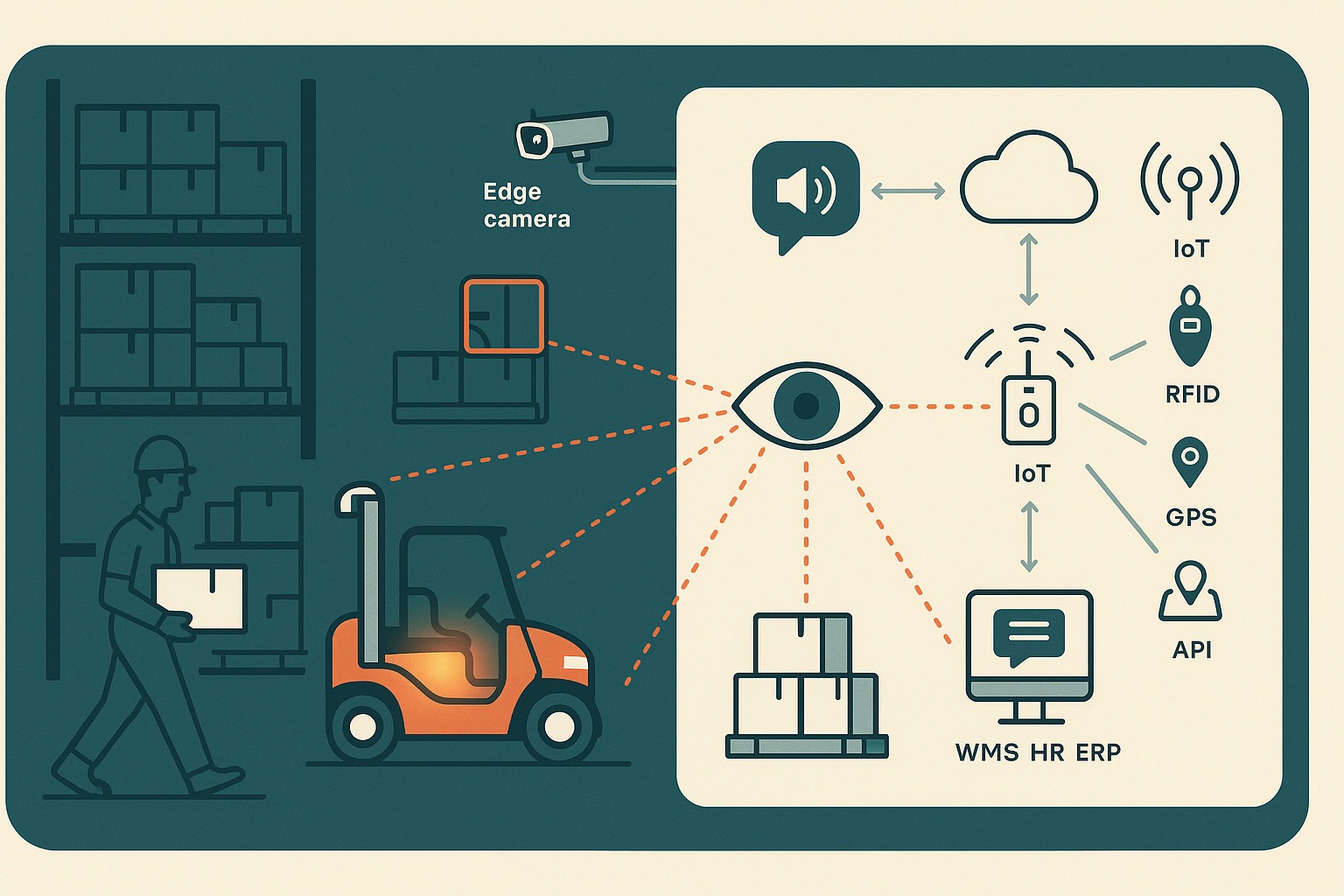
- Computer Vision (CV): Core for all modules that analyze video – from facial recognition for attendance to object detection for counting and surveillance. Modern CV models (e.g. YOLO, SSD) process live video streams to identify people, safety gear, and inventory items.
- Deep Learning & ML: Convolutional Neural Networks and other AI models power classification and prediction (e.g. stress level detection, anomaly detection in telematics). These models are trained on warehouse-specific data to improve accuracy over time.
- Thermal Imaging: Infrared cameras capture equipment heat signatures. AI analyzes thermal patterns to pinpoint overheating parts – a technique proven in maintenance programs.
- IoT & Sensors: RFID, BLE, GPS, and other sensors on trucks, pallets, and equipment feed real-time data. Telemetry platforms aggregate this IoT data (battery stats, location, usage) enabling predictive analytics.
- Speech Synthesis (TTS): Converts text alerts into natural-sounding voice notifications for instant worker feedback. High-quality TTS engines ensure clear, multi-language announcements.
- Edge/Cloud Integration: Many computations (e.g. initial image detection) run on edge devices/cameras, while heavier tasks (model retraining, dashboards) occur in the cloud. Secure APIs connect modules to existing systems (WMS, HR, ERP) for end-to-end automation.
These components combine to form a robust architecture. For example, a single module might use CV for data capture, ML for decision-making, and APIs to sync results. The true power emerges when these technologies interoperate across modules: attendance logs feed into HR systems, counting feeds into inventory, and CCTV systems tie into safety alerts in one unified platform.
Potential Impact & Benefits for Warehouses (Modular & Integrated)
Deploying AI modules brings concrete operational gains, whether rolled out incrementally or as a unified system:
- Automated Compliance & Safety: Continuous vision-based monitoring ensures PPE, access rules, and vehicle operations are followed. Real-time alerts improve safety and help avoid fines or accidents.
- Labor & Cost Savings: Mundane tasks (attendance logging, paper keying, manual counts) are automated, freeing staff for higher-value work. This reduces overtime and error-related costs.
- Enhanced Accuracy: AI reduces human errors – weights and counts become exact, inventories stay synchronized, and GRN entries match physical deliveries. Consistency improves across shifts and sites.
- Theft & Loss Prevention: Integrated surveillance and RTI tracking deter unauthorized removal of goods. AI detection of suspicious behavior has been shown to reduce shrinkage in smart warehouses.
- Faster Throughput: Processes like goods receipt and shipping checks accelerate, since data flows automatically. For example, CV-based box counting speeds up loading docks by confirming pallet loads in real time.
- Predictive Maintenance: Monitoring equipment temperature and battery health lets managers schedule maintenance proactively. This minimizes downtime and extends asset life.
- Real-Time Visibility: Managers gain dashboards with live data: who’s on shift, where each truck and pallet are, and which processes are stalled. This transparency drives quicker decisions and optimized workflows.
- Scalability & Flexibility: The modular platform scales to multiple sites. Start with core issues (e.g. attendance+security), then add modules (counting, health) as needed. Each AI component independently delivers ROI, and together they compound efficiency.
- Better Worker Experience: Automated attendance and safety alerts create a fairer, more predictable environment. Prompt reminders (voice or screen) help workers comply without time-consuming meetings or reprimands.
In essence, AI for Warehouse Management turns visual and sensor data into actionable intelligence, enabling smart warehouse solutions that were impossible with legacy methods. This leads to measurable improvements in productivity, safety, and cost control across any logistics-heavy enterprise.
Important Considerations for Implementation
Adopting an AI-driven warehouse platform requires careful planning:
Data Requirements:
Integration Complexity:
Model Training & Maintenance:
Infrastructure:
Worker Privacy & Acceptance:
Environmental Factors:
Safety and Ethical Use:
By addressing these factors, organizations ensure the AI modules operate reliably and add value. Softlabs Group’s team can guide you through these steps, tailoring each component to your site’s specifics while respecting legal and ethical standards.
Tailoring AI for Your Unique Needs with Softlabs Group
The AI modules described above are powerful on their own, but their true potential is unlocked when integrated into a bespoke warehouse intelligence platform. Softlabs Group specializes in custom AI solutions – from developing individual computer vision models to orchestrating a unified system. We work closely with your team to align each module with your workflows, existing software, and business rules.
Whether you need to start with a pilot (for example, automating attendance and GRN processing) or envision a full-scale rollout (combining all modules for a “lights-out” warehouse), Softlabs can deliver. Our experts will conduct thorough assessments of your current infrastructure, set up the data pipelines (camera feeds, sensors, databases), and iteratively refine the AI models on your data. We also handle system integration (linking to HR, WMS, ERP) and ensure scalability for future expansion.
Choose Softlabs Group for a custom AI-powered warehouse solution and transform your operations with cutting-edge automation. Reach out today to discuss how our warehouse AI platform can be designed and deployed for your logistics environment, unlocking efficiency and insight tailored exactly to your needs.